-
American Society for Testing and Materials (ASTM) defines textile materials as
Fibers, yarn intermediates, yarns, fabrics, and products made from fabrics which retain more or less completely the strength, flexibility, and other typical properties of the original fibers or filaments
-
Polymer
a long chain molecule (macromolecule)
-
Fiber
unit of matter having an extremely small diameter and a length at least 100 times the diameter
-
Yarn
a continuous strand of textile fibers, and filaments
-
Fabric
a thin sheet that is formed by interlaced, interloped, or knotted yarns, or by distributed fibers that are held together mechanically or chemically
-
Examples of physical properties
thermal, moisture, specific gravity
-
Examples of chemical properties
resistance to acid, alkali, oxidizing
-
Examples of acidic chemical properties
hydrochloric, sulfuric, nitric acids, acetic acids
-
Examples of basic chemical properties
sodium, potassium, and ammonium hydroxides
-
Examples of mechanical properties
stress-strain, resilience, flexibility
-
The most important atoms in fiber-forming materials
Carbon, Hydrogen, Nitrogen, and Sulfur
-
Macromolecule
- a large molecule commonly created by some form of polymerization
- Four conventional biopolymers: nucleic acids, proteins, carbs, and lipids
-
Polymerization
- Monomer --> polymer
- Ex: ethylene --> polyethylene
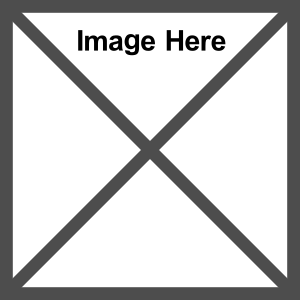 - Ex: Propylene --> polypropylene
- Ex: Styrene --> polystyrene (styrofoam)
- No by-products are produced
-
Monomer
individual units in polymer
-
Backbone
- carbon atoms covalently bonded to each other or oxygen or nitrogen
- -C-C-C- , -C-O-C- , -C-N-C-
-
Attached groups (polymerization)
- Hydrogen (-H)
- Methyl (-CH3)--Hydrophobic
- Hydroxyl (-OH)--Hydrophilic
-
-
Addition (chain-growth; in polymerization)
direct coupling of two identical monomers, unstable bonds (double bond)
-
Initiator (polymerization)
breaks a double bond
-
Radical (radioactive; in polymerization)
breaks more double bonds (in addition to initiator)
-
Polypropylene (PP)
- thermoplastic polymer, made by the chemical industry and used in a wide variety of applications
- An addition polymer, made from the monomer propylene, is rugged and unusually resistant to many chemical solvents, bases, and acids
-
Polystyrene
thermoplastic substance, which is in solid (glassy) state at room temperature, but flows if heated above its glass transition temperature (for molding or extrusion), and becomes solid again when cooled
-
Polyvinyl alcohol
- used as an emulsion polymerization aid, as protective colloid, to make polyvinyl acetate dispersions
- One of the largest market applications in China
-
Polyvinyl chloride (PVC)
- thermoplastic vinyl polymer constructed of repeating vinyl groups (ethenyls) having one of their hydrogens replaced with a chloride group
- third most widely produced plastic, after polyethylene and polypropylene
- Widely used in construction because it's cheap, durable, and easy to assemble
-
How can PVC be made softer and more flexible?
By addition of plasticizers, the most widely used being phthalates
-
Condensation
- Step-growth
- directly coupling two different monomers (reactive groups)
- the formation of covalent bonds in polymer chains produces by-products
-
Degree of polymerization (n)
the number of monomer units present in a polymer
-
Polymer type (basic)
[], O represent two different monomers
-
Homopolymer
one monomer -[]-[]-[]-[]-
-
Copolymer
two monomers -[]-O-[]-O-
-
Block polymer
two or more homopolymers -([])n-(O)m-
-
Extrusion (synthetic fiber formation)
forcing or pumping the spinning solution through the tiny holes of a spinneret
-
Spinning (synthetic fiber formation)
extruding a liquid polymer solution through one or thousands of holes in a spinneret
-
Three major types of spinning man-made fibers
- Melt spinning
- Dry spinning
- Wet spinning
-
All the major types of man-made fiber-spinning techniques have
- a reservoir and a metering pump
- spinning jet (spinneret)
- take-up device to draw filaments and wind them onto a package
-
Melt spinning
- thermoplastic polymers
- resin solids are melted in autoclave
- fiber is spun out into the air
- fiber solidifies
- least expensive
- Ex: nylon, polyester
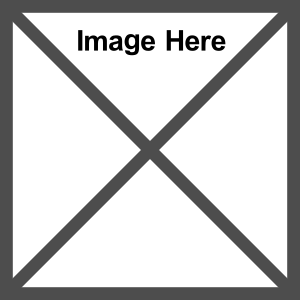
-
Drawing and orientation
- while extruded fibers are solidifying, or in some cases after they have hardened, the filaments may be drawn to impart strength
- Drawing pulls the molecular chains together and orients them along the fiber axis, creating a considerably stronger yarn
-
Dry (solvent) spinning
- polymer is dissolved in solvent
- extruded into a hot gas where filaments are hardened
- solvent evaporates and is recycled
- Ex: acrylics, acetate
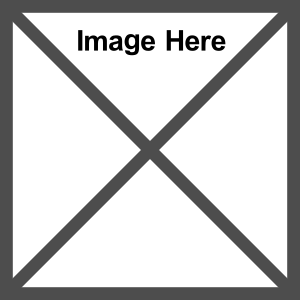
-
Wet spinning
- polymer is dissolved in suitable solvent
- extruded into a liquid bath, where filaments coagulate
- Ex: viscose, rayon, acrylics
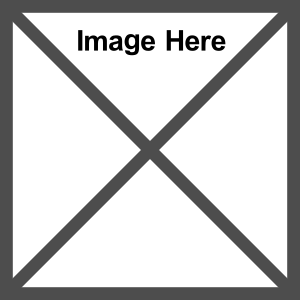
-
Most synthetic and cellulosic manufactured fibers are created by
extrusion
-
Extrusion
forcing a thick, viscous liquid through the tiny holes of a device called a spinneret to form continuous filaments of semi-solid polymer
-
What types of polymers need to be melted in order to become fluid?
thermoplastic synthetics
-
What types of polymers need to be dissolved in order to become fluid?
Non-thermoplastic cellulosics
-
Bicomponent fibers
- consists of two polymers that are chemically and/or physically different
- Ex: side by side; matrix fibril; sheath core
-
Crystalline region (fine structure)
- polymers are tightly packed, ordered
- Mechanical properties such as strength, stiffness, etc.
- (Rc)
-
Amorphous region (fine structure)
loose, disordered
-
Chemical properties (fine structure)
dyeability, absorbancy, etc. (Ra)
-
Crystallinity (fine structure)
- the property of crystalline to amorphous regions
- C = Rc / (Rc + Ra)
-
Orientation (fine structure)
- directions of polymer chains relative to the longitudinal axis of the fiber
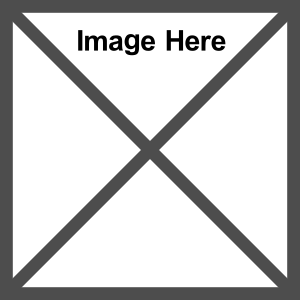
-
The higher degree of orientation and crystallinity of a polymer chain...
the stronger, stiffer, less stretchable, less absorbent
-
Van der Waals force
neutral molecular attractions due to very weak electrostatic forces
-
Dipole-dipole interaction
- positive end of one polar molecule to the negative end of another polar molecule
- Ex: the attraction occurring between hydrogen atoms on one molecule with strongly electronegative atoms on another molecule (chlorine, fluorine)
-
Hydrogen bond
a strong dipole-dipole attraction occurring between hydrogen on one molecule and oxygen and nitrogen on another molecule
-
Covalent crosslinks
- an atom on one polymer chain and an atom on the adjacent polymer chain due to the sharing of electrons
- Ex: disulfide bonds in wool polymers
-
Tensile test
behaviors under a pulling force along the fiber axis
-
Strength (fiber property)
resistance to deformation developed within a fiber being subjected to a tensile force (gram or Newton)
-
-
Stress (tenacity)
stress expressed as a force per linear density (gram/denier or Newton/tex)
-
Linear density
coarseness/fineness of fibers or yarns
-
Tex
- Tex = grams / 1000 m
- Tex = 9 x denier
-
Denier
- Denier = grams / 9000 m
- Denier = Tex / 9
-
Elongation (strain)
- deformation (elongation) by a tensile force
- strain is the percent of elongation vs original length (%)
-
Strain (formula)
- Strain = E / L0 x 100%
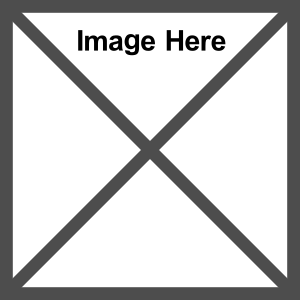
-
Initial modulus
- the initial portion of the stress-strain curve is straight
- the slope of the line is called initial (Young's) modulus
- IM indicates how easily the fiber extends under small stress
-
The larger the Initial Modulus...
the stiffer and less extendible
-
Yield point
- the point at which the stress-strain curve flattens
- Permanent change in fiber structure and permanent deformation occurs
-
Rupture point (breaking point)
Catastrophic change in structure (polymers massively either slip or rupture)
-
Breaking tenacity
the maximum stress
-
Breaking elongation
the maximum strain
-
Elastic recovery
- a strained fiber contracts as the applied stress decreases
- Before the yield point, the fiber acts like a spring, 100% recovery
- Beyond the yield point partial recovery through a different path
-
Moisture regain
- the amount of moisture the fiber contains when placed in an environment at a certain temperature and relative humidity
- MR = (W - Wb) / Wd x 100%
- W=weight at standard condition
- Wd=weight in the dry condition
-
Standard testing conditions
70oF and 65% RH
-
Standard MR for wool
15~16%
-
Standard MR for Rayon
12%
-
Standard MR for cotton
8.5%
-
Standard MR for acetate
6.5%
-
-
Standard MR for acrylic
1.5%
-
Standard MR for polyester
0.4%
-
Standard MR for polypropylene
0%
-
Which kind of fiber needs the highest MR (15~16%)?
Wool
-
Which kind of fiber needs the lowest MR (0%)?
Polypropylene
-
Swelling (absorption of liquid water)
a percent increase in diameter
-
Dimensional change (absorption of liquid water)
shrinkage in length
-
Tenacity (absorption of water)
- hydrophilic fibers except cotton and flax become weaker
- hydrophobic fibers are not or less affected by water
-
Stiffness (absorption of water)
decreases with water absorption
-
Heat of wetting
- the amount of heat that evolves in water absorption
- It influences comfort
- When a person goes from an environment of low relative humidity into one of higher relative humidity, he/she will receive that heat
-
Specific heat
a measure of the amount of heat require to change the temperature of a unit mass of the fiber by 1oC
-
Thermal conductivity
a measure of the rate of heat flow through the fibers
-
Glassy-->rubber glass transition temperature
bonds in the amorphous regions are broken up
-
Melting temperature
bonds in the crystalline regions are broken up
|
|