-
TEXTILE PRODUCTS
Textiles (fiber, yarn, fabric), Apparel, Home Furnishing (upholstery, floor covering, drapery, wall covering), Industrial (tents, awnings, hose, tire cord, geotextiles)
-
SERVICEABILITY
Fitness to consumers' needs (aesthetic, comfort, economic...); Durability (lifetime); Maintenance (machine washing, dry-cleaning, hand-washing)
-
POOR QUALITY COSTS
Individual Consumer; Retailer; Manufacturer
-
APPROACHES OF TEXTILE TESTING
- Service Testing (Test samples/products in a real life situation; Simple, but takes a long time, because you have to wait a few days/months to see changes)
- Laboratory Testing (Reliable, accurate, but indirect; accelerated testing - create a device to simulate what's going on when you wear the garment; separate machines)
-
GOALS OF TEXTILE TESTING
- Conformance to specifications set by standards
- Quality control
- Product improvement
- Adherence to government regulations
- Forensic testing
-
SELECTION CRITERIA
- Appearance (color, style, texture, ...)
- Comfort (hand: soft vs hard, smooth vs rough, cool vs warm)
- Price
- Serviceability
- Maintenance
- Safety
-
STANDARDS
Specifications for end use; A precise statement of a set of requirements to satisfied by a material, product, system or service, indicating whenever appropriate, the procedure by means of which it may be determined whether the specified requirements have been met.
-
Testing methods (Eight sections)
- 1. Scope: what particular products, exclusion;
- 2. Referenced Documents: standard testing methods
- 3. Definitions: ASTM D123
- 4. Uses and Significance: voluntary; some requirements can be modified.
- 5. Sampling: at the time to reach the user; number., size and direction of samples,
- 6. Specification Requirements: characteristics, requirements and testing methods.
- 7. Testing Methods: details for carrying out the tests.
- 8. Indexing Term
-
RELIABLE TEST
Reliability, consistency, reproducibility, dependability
-
Precision vs Accuracy
- Precision: the degree of agreement within a set of tested results
- Accuracy: the degree of agreement between tested results and the true value.
-
STANDARDIZATION ORGANIZATIONS
- Individual companies, government organizations and industry associations.
- National standard-setting organizations: AATCC, ASTM, ANSI.
- International standard-setting organizations: ISO
-
ISO
- International Organization for Standardization
- international standard-setting organization
-
AATCC
- American Association of Textile Chemists and Colorists
- National standard-setting organization
-
ASTM
- American Society for Testing and materials
- National standard-setting organization (not for profit; semi-governmental)
-
ANSI
- American National standard Institute
- a voluntary federation of standards-developing and standards-using organizations
- Representative of USA in the international organization
-
FACTORS INFLUENCING TEST RESULTS:
- Observer Reading scale
- Equipment
- Environment
- Material
- Data Analysis
-
How the observer reading the scale can influence test results
- parallax error; round off, subjective evaluation
- Round off
-
Errors in observer's subjective evaluation which affects test results
- Change in color, pilling, wrinkling, etc.
- Training; multiple reading (>3 ratings)
-
How the equipment can influence test results
- Maintenance: to keep in good condition
- Calibration: to adjust the setting to give correct results
- Verification: checking or recalibration
-
How the environment can influence test results
- Temperature: equivalent to the amount of energy in the motion of atoms and molecules
- Humidity: amount of vapor present in the air (%)
- Relative Humidity (RH): The amount of vapor in the air at a given temperature, compared to the maximum limit the air can hold at the same temp
-
Moisture regain
The percentage of water weight contained in the specimen
-
Standard RH for testing
65+2 %
-
How material can influence test results
- Sampling Rules: random, no bias.
- 1. Do not take specimens from selvage edges. 4 inch margin should be given on both sides of the fabric.
- 2. Do not take specimens for one test that contain the same yarns. For the purpose of practicing, a warp wise sample may contain the filling yarns, vice verse.
- 3. Mark and cut specimens accurately and on-grain. Markers (test No. and direction) should be small and away from critical areas.
-
Standard Temperature for testing
70+2 oF (21+1oC)
-
Conditioning
the process of acquiring moisture and temperature equilibrium with standard atmospheric conditions
-
How data analysis can affect test results
- Presentation of raw data: table and figure
- Statistics: Mean, Variance, Standard Deviation, Coefficient of Variance
-
Mean formula (statistics)
X = (Σx) / N
-
Variance formula (statistics)
v - [ Σ (x - X)2 ] / (N-1)
-
Standard deviation formula (statistics)
S = √V
-
Coefficient of variance formula (statistics)
CV = S / X
-
FABRIC PARAMETERS
- Closeness
- Balance
- Thread count
- Yarn size (Direct system, Indirect system)
- Cotton Count
-
Closeness (fabric parameters)
ratio of the area covered by threads to that of the area of a fabric.
-
Balance (fabric parameters)
equal number of warps and fillings in a unit area.
-
Thread Count (fabric parameters)
- Number of yarns per inch; warps x fillings: 78 x 68
- Thread count is defined as number of yarns per unit length of the fabric
- Thread count is also sometimes defined as the total number of yarns in one square unit of the fabric
-
Yarn Size in a direct system
- numerical expression which defines fineness of a yarn
- Yarn size is expressed in the direct system is directly proportional to the linear density of the yarn
- linear density = mass / length
-
Tex (yarn size)
- grams per 1000 meters of yarn
- 1 tex = 9 denier
-
Denier (yarn size)
- grams per 9000 meters of yarn
- 1 tex = 9 denier
-
Yarn size in an indirect system
- Inversely proportional to the linear density of the yarn.
- measures length per unit mass
- linear density = length / mass
-
The higher the yarn size (Tex/Denier/American grain count) in a direct system, the ______ the yarn
coarser/heavier
-
A 200m length of yarn weighs 5g. Find its Tex.
- Tex = g / 1000m
- 5g / 200m = x / 1000m
- 5 g x 1000m = 5000
- 5000 / 200 = ****25 g/m****
-
A 200m length of yarn weighs 5g. Find its denier.
- Tex = 25 g/m
- 1 tex = 9 denier
- Denier = 9 x 25 = ****225 g/m****
-
The higher the yarn size (cotton count/worsted count/linen lea/yarns per pound/metric count)in an indirect system, the _____ the yarn
finer/lighter
-
Find the cotton count for a 200 yd sample which weighs 0.01 lb.
- Cotton count = # of 840 yard lengths per pound
- 200 / 0.01 = 20,000
- 20,000 / 840 = ****23.81***
-
Cotton count
# of 840 yard lengths per pound
-
Yarn twist (fabric parameters)
- In spinning, Twist refers to the turns inserted into a yarn to bind its fibers together
- Twist present in the yarn can be expressed in terms of Turns per inch (TPI) or Turns per meter (TPM)
-
Consider two yarns A and B. Yarn A has 18 TPI and yarn B has 20 TPI. Which yarn is harder twisted?
B
-
Consider two yarns A and B. Yarn A has a cotton count of 36 and 18 TPI, and yarn B has a cotton count of 64 and 20 TPI. Which yarn is harder twisted?
- Twist factor = TPI / √Cotton Count
- Yarn A twist factor = 18 / √36 = 18 / 6 = 3
- Yarn B twist factor = 20 / √64 = 20 / 8 = 2.5
- ****A****
-
Twist angle
- the angle between a tangent to the helix formed by the fiber and the yarn axis.
- Twist angle determines the hardness of twist, i.e. it tells us whether the yarn is soft twisted or hard twisted
- Only TPI cannot tell whether the yarn is soft twisted or hard twisted
-
Twist angle depends on...
TPI and yarn size (Tex, denier, cotton count, worsted count, etc.)
-
Twist factor or Twist multiplier
- represents hardness of the twist.
- proportional to the tangent of twist angle (tan θ)
-
In Direct system: Twist Factor =
- Twist Factor = TPM x √Tex
- Twist Factor = TPM x √Denier
-
In Indirect system: Twist Factor =
Twist Factor = TPI / √Cotton Count
-
The higher the twist factor...
the harder the twisted yarn
-
A test to find the twist direction
- Rotate the right end of a small yarn sample in the clockwise direction.
- If it results in untwisting the yarn then the yarn has Z-twist
-
Untwist to Break (yarn twist measurement)
- A specimen is untwisted until it breaks.
- It is assumed that when the yarn breaks it has no twist.
- Twist, as turns per unit length, is calculated as the number of turns registered on the counter divided by the specimen length
-
Twist contraction method (yarn twist measurement)
- A specimen is untwisted and then re-twisted in the opposite direction until it contracts to its original length.
- It is assumed that the same amount of twist has been inserted as was originally present.
- Twist, as turns per unit length, is calculated as half the number of turns registered on the counter divided by the specimen length
-
Twist to break method (yarn twist measurement)
- Applicable when the earlier two methods fail.
- Two yarn samples are required
- First yarn sample is untwisted and then re-twisted until it breaks
- Second yarn sample is twisted until it breaks
- Twist, as turns per unit length, is calculated as half of the difference in turns registered on the counter for the first and second yarn sample, divided by the specimen length.
-
Surface density (fabric weight) =
Mass / area
-
Fabric weight (fabric parameters)
weight per unit area (g/mm2, oz./yd2)
-
Fabric Thickness measured using
a Compressometer
-
FLAMMABILITY
Relative ease of ignition and relative ability to sustain combustion.
-
Flame-resistance
flaming combustion is prevented, terminated, or inhibited with or without subsequent removal of the ignition source.
-
Flame-retardant
finish to impart flame-resistance.
-
Factors affecting flame-resistance
- Fiber content
- Fabric weight per unit area
-
Fiber content affecting flame-resistance
- Cellulosic fibers such as cotton, flax, viscose have low flame resistance rating
- Woolen fabrics usually have high flame resistance rating
- Thermoplastic fibers shrink from the flame and tend not to ignite
-
Fabric weight affecting flame-resistance
the heavier the fabric, the greater the flame resistance rating
-
Flame Spread Time
- The time taken by a flame on a burning material to travel a specified distance under specified conditions.
- > 7s : Class I
- 4 - 7s : Class II
- < 4s : Class III Fabrics.
-
Crease
desirable residual bending deformation in garments.
-
Wrinkles
undesirable residual bending deformations in garments.
-
Crease and wrinkle recovery
the property of fabric which enables it to recover from being folded and from forming undesirable wrinkles
-
Wrinkle resistance (resilience)
ability to absorb energy without permanent deformation
-
Wrinkle recovery (resilience)
The power to recover original shape a size after removal of the strain which caused the deformation
-
Resilience
A fiber may possess this quality to spring back to its original state after being wrinkled
-
Factors affecting Crease and Wrinkle Recovery
- Crease Recovery Test: recovered angle
- Wrinkle Recovery Test: Appearance
-
Fiber content affect Crease and Wrinkle Recovery
- Cellulosic materials are notoriously susceptible of creasing
- Decreasing order of crease resistance:
- Wool--Silk--Acetate--Nylon--Viscose rayon--Cotton--Flax
-
Fiber length affecting Crease and Wrinkle Recovery
Very short fibers tend to be displaced easily when yarns are folded therefore retain permanent deformation
-
Fiber Geometry affecting crease and wrinkle recovery
- Round x-section fibers resist bending and usually recover quickly from light to medium folding stresses
- Nevertheless, they recover slowly if heavy wrinkles are formed
-
Yarn twist affecting crease and wrinkle recovery
- Low twisted yarns allow fiber displacement thereby showing poor recovery
- Yarns of medium twist provide littler or no opportunity for fiber displacement, so these yarns tend to return to their original position
- High twisted yarns under heavy wrinkles show poor recovery due to stresses and strains that tend to hold the structure
-
Yarn mobility
- ability to move in the fabric
- Loose structure allows high mobility
-
Type of weave affecting crease and wrinkle recovery
Woven fabrics of basket, twill or satin-weave constructions recover more easily from wrinkles (due to higher yarn mobility) than plain-weave fabrics
-
Thread count affecting crease and wrinkle recovery
low thread count fabric structures have higher yarn mobility than high thread count fabric structures thus recover more easily from wrinkles
-
DRAPE
- The way a fabric hangs.
- The property which permits a material to orient itself into graceful folds when acted upon by force of gravity.
- Fabric stiffness (resistance to bending) is a key factor in study of drape
- Affected by yarns, weave structure and finish
-
Drape coefficient measurement
shadow
-
Cantilever test
bending length c to find drape
-
Relationship between Twist Factor and Fabric Stiffness
- Fabric Stiffness is directly proportional to Twist Factor (yarn twist and linear density)
- In direct system:
- TPM x √Tex
- TPM x √Denier
- In indirect system:
- Twist Factor = TPI / √Cotton count
-
Drape coefficient relating to fabric stiffness
High Drape Coefficient signifies stiffer fabric
-
Relationship between overhang length and bending length in Cantilever test
Higher overhand length in Cantilever test translates to stiffer fabric
-
Relationship between Heart Loop length and fabric
Higher length in Heart Loop test translates to limper fabric
-
Flexural Rigidity
- work per unit width which is required to bend a fabric to unit radius of curvature
- G = 3.39w1c3 mg - cm
- G = w2c3 x 103 mg - cm
- w1 = fabric weight in oz per yard2
- w2 = fabric weight in grams per cm2
- c = bending length
-
Bending modulus
- Measure of stiffness and is independent of the dimensions of the strip tested and may be regarded as the "intrinsic stiffness"
- Used to compare the stiffness of the material in fabrics of different thicknesses
- q (kg/cm2) = 732G / g13
- q (kg/cm2) = (12G x 10-6) / g23
- g1 = fabric thickness in thousandths of an inch
- g2 = fabric thickness in cm
- G = flexural rigidity
-
PILLING
- Pills are bunches or balls of tangled fibers which are held to the surface of a fabric
- Fabric surface fault characterized by little fiber balls or pills of entangled fiber clinging to the cloth surface and giving the garment an unsightly appearance
-
3-stage development of pilling
- Development of surface fuzz
- Tangling of the fuzz into pills
- Breaking away of pills
-
How fiber can affect Pilling
- Length: Short fibers have more loose ends that easily protrude from yarn structure, causing more pilling (ex: staple vs. filament yarns)
- Surface characteristics: Smooth fibers show less pilling as compared to fibers with rough surfaces (nylon vs. wool)
- Strength: high strength fibers hold pills on fabric surface more firmly, resulting in more visible pilling (Ex: use of special low strength polyester fibers in woolen blends to reduce pilling)
-
How yarns can affect Pilling
- Twist: highly twisted yarn structures hold fibers more firmly, resulting in less pilling
- Linear Density (tex, denier): yarn with higher linear density and generally coarse yarns pill more
-
How fabric structure affects Pilling
- Type of weave: plain weave pills less than other basic weave types (ex: twill and satin weave)
- Thread count: high thread count structures are more compact and pill less
-
Factors affecting Pilling
Fiber, yarn, fabric structure
-
Shrinkage (dimensional stability)
Transverse swelling,longitudinal shrinkage
-
Test for dimensional stability
Regular washing and drying cycles with the fabric specimen
-
Types of shrinkages
Relaxation, Consolidation, Felting, Heat or Thermal, Progressive
-
Growth
Increase in fabric dimensions
-
The Shrinkage Theory
- After wetting, filling yarns swell and warp yarns stretch to accommodate them, and warp yarns relax to relieve the stress, bringing the yarns closer together
- Transverse swelling (submerged in water), longitudinal shrinkage
-
Formula to measure shrinkage
S = [(L - L0) / L0] x 100%
-
Soiling
'overall' contamination or discoloration of a material.
-
Staining
'local' contamination or discoloration of a material.
-
Surfactant
wetting agent. Lower the surface tension of the water, loosen, surround, and suspend the soil. Polar molecules. They have heads that are hydrophilic and tails that are hydrophobic (water-hating).
-
Roll-up process:
- Wetting (water and surfactant molecules penetration)
- Breaking up (small sizes)
- Separation (oil-fabric interface formation)
- Rolling up
- Suspension
- Redeposition
-
Soiling and Fiber geometry: Fibers with smooth surface, relatively large diameter, made into smooth yarns and firm fabrics...
tend to resist soiling
-
Soiling and Fabric Geometry: Fabrics with loose structure...
tend to permit penetration of soil into the interstices
-
Soiling and Fabric Geometry: Fibers with irregular cross-sections...
provide spaces for soil particles to settle in and hinder their removal
-
Soiling and Fabric Geometry: Loosely twisted yarns that are somewhat coarse...
are readily penetrated by soil
-
Soil release finishes: Oily stains
- Their removal is primarily dependent upon the hydrophobicity of the fibers
- Wetting finishes helps water to diffuse between the oil/fiber interface, and thus facilitate removal of oil substances
-
Soil release finishes: Solid soils
- Their deposition does not depend upon the hydrophobicity of the fibers
- It depends upon the adhesion of solid particles to the fiber that is caused by Van der Waal's forces and on the contact area between the fiber surface and the particle
- The contact area between the fiber surface and the particle is influenced by surface, texture, irregularities, fuzziness, weave
- Removal of solids from fiber surface requires breaking the adhesive bound between fiber and solid, followed by separation of two surfaces by wetting
-
Wetting in the Roll-up process
- Surfactant: is wetting agent.
- Lower the surface tension of the water, loosen, surround, and suspend the soil.
- Surfactants are molecules made up of two parts.
- They have heads that are hydrophilic (water-loving) and tails that are hydrophobic (water-hating).
-
Rolling up step in Roll-up process
As the hydrophobic tail of a surfactant tries to cling to a surface, it forces itself underneath layers of soil, loosening and lifting it from the surface.
-
Suspension step in Roll-up process
- As the cleaning solution rolls up bits of dirt and soil, the surfactant's hydrophobic tails cling to the particles because they're not water.
- The soil is held suspended in the cleaning solution by the power of the surfactant, keeping it from settling back on your countertop.
- Once the surface is clean, you simply wipe and dry.
-
Repellent finishes
- These finishes function by coating the fiber surface to increase its surface tension below that of liquids would wet the fiber. This limited wettability would prevent the unwanted liquid from residing on the fiber surface.
- These finishes are also effective in preventing or minimizing adhesion of particulate matter to fibers.
-
Waterproof fabric
- fabric coated or impregnated with fats, waxes, rubber to form a continuous wall against the passage of water
- Waterproof fabric has low degree of permeability.
-
Water resistant fabric
Water resistance is the ability of a fabric to resist wetting and penetration of water.
-
Water repellent fabric
- Water repellency is the property of fiber, yarn or fabric characterized by its resistance to wetting by water.
- A water repellent fabric is one whose fibers are usually coated with a hydrophobic compound and whose pores are not filled in the course of treatment.
- This type of fabric is quite permeable to air and water vapors.
-
Basic concept of wetting and water repellency
- High surface tension beads up liquid.
- Water is polar (postively and negatively charged.
- When solid surface has polar molecules, water can be attracted and spread--wetting
- WR finish improves contact angle to increase surface tension.
-
Surface tension
a tendency to minimize surface area of liquid on a solid surface.
-
Contact angle
Angle between the solid surface and the tangent of the water surface as it approaches the solid, the angle being measured in water.
-
Water Repellency Test
rain test
-
Munsell color system
a color space that specifies colors based on three color dimensions, hue, value (lightness), and chroma (color purity or colorfulness).
-
Munsell book
- actual swatches or chips of colored materials.
- Differences among adjacent chips have been made nearly constant visually
- Ten hues: R, YR, Y, GY, G, BG, B, PB, P, RP. Four pages are used for shades of each hue (2.5, 5, 7.5, 10)
- Value: 1 (black) ~ 10 (white)
- Chroma: 0 (gray) ~16 (more colorful)
- Notation: 7.5 YR 3/12
-
Hue (Munsell color system)
- Each horizontal circle Munsell divided into five principal hues: Red, Yellow, Green, Blue, and Purple,
- along with 5 intermediate hues (YR, GY, BG, PB, RP) halfway between adjacent principal hues.
- These 10 steps are then broken into 40 sub-steps, (2.5, 5, 7.5, 10).
- Two colors of equal value and chroma, on opposite sides of a hue circle, are complementary colors, and mix additively to the neutral gray of the same value.
- The diagram below shows 40 evenly-spaced Munsell hues, with complements vertically aligned.
-
Value (Munsell color system)
- Value, or lightness, varies vertically along the color solid, from black (value 0) at the bottom, to white (value 10) at the top.
- Neutral grays lie along the vertical axis between black and white.
-
Chroma (Munsell color system)
- Chroma, measured radially from the center of each slice, represents the 'purity' of a color, with lower chroma being less pure (more washed out, as in pastels).
- Note that there is no intrinsic upper limit to chroma.
- Different areas of the color space have different maximal chroma coordinates.
- For instance light yellow colors have considerably more potential chroma than light purples, due to the nature of the eye and the physics of color stimuli.
- This led to a wide range of possible chroma levels--up to the high 30s for some hue-value combinations (though it is difficult or impossible to make physical objects in colors of such high chromas, and they cannot be reproduced on current computer displays).
-
How is a color fully specified?
- by listing the three numbers for hue, value, and chroma.
- For instance, a fairly saturated purple of medium lightness would be 5P 6/10 with 5P meaning the color in the middle of the purple hue band, 6/ meaning medium lightness, and a chroma of 10.
-
CIE L*a*b* system
- L*-lightness
- a*- redness(positive)--greenness (negative)
- b*- yellowness(positive)--blueness(negative).
-
Colorfastness
The property of a dye or a print to retain its hue throughout the wear life of a product.
-
Crocking
- the degree of color transfer from one colored textile material to another by rubbing.
- A standard white cotton fabric is used for all crocking tests
-
Colorfastness to Perspiration test method
AATCC 15: Fabric attached to multi-fiber fabric is dipped in the perspiration solution (pH 4.3+2) for 20-30 minutes and then heated in the oven for at least 6 hrs maintained at 38+1o C (100+2o F).
-
Colorfastness to Washing test method
AATCC 61: Multi-fiber fabric is used to see how much color is transferred (staining scale) and then the original specimen is compared to an unwashed specimen to see how much color is lost (gray scale).
-
Tensile Strength test
subjected to a longitudinal pulling force.
-
Tensile strength
- The maximum resistance of material to deformation in a tensile test (carried till the material ruptures).
- Units: lbf, kgf, Newton (N)
- The amount of pulling a fiber can withstand before it stretches and breaks.
- It is a measure of the steady force required to break a yarn i.e. breaking load
-
Stress
- 'strength per unit cross sectional area'.
- Stress = Load / Area.
- But the cross sectional area does not remain constant throughout the length of yarns.
- It is the 'Linear density' of yarn which remains more or less constant throughout the yarn length.
- So we will use the following measure to compare the strength of two different yarns
-
Specific stress
- 'Load per unit Linear Density'
- Specific Stress = Load / Linear Density
-
Tenacity
- The maximum stress developed in a specimen stretched to rupture is called Tenacity.
- Tenacity = Breaking Load / Linear Density
-
Elongation
Increase in length of a specimen under some load is called elongation.
-
Strain
- ratio of elongation to the original length.
- Strain = Increase in Length / Original Length.
- Generally, Strain is expressed as the amount of elongation as a percentage of original specimen length.
- Strain (%) = (Increase in length x 100) / original length
-
Breaking elongation
- elongation required to break a yarn
- Breaking strain = breaking elongation / original length
- To make comparison between the specimens of different original length, use strain over elongation
-
Breaking strain
- strain required to break the yarn
- Breaking strain = change in length at break / original length = breaking elongation / original length
- To make comparison between the specimens of different original length, use strain over elongation
-
A 20 cm long yarn has breaking elongation of 40 mm. Find out breaking strain.
- 40 mm = 4 cm
- Breaking strain = Breaking elongation / original length
- = 4 cm / 20 cm = ****0.2 cm****
-
A 20 cm long yarn has breaking elongation of 4 cm and 10 cm long yarn has a breaking elongation of 3 cm. Which yarn will give more extensible/stretchable fabric ?
- Breaking strain = Breaking elongation / original length
- A: BS = 4 / 20 = 0.2 cm
- B: BS = 3 / 10 = 0.3 cm
- ****Second yarn is more stretchable and has higher strain****
-
Work of rupture (toughness)
- the energy required to break a yarn and is also known as Toughness.
- The work of rupture is given by the total area under the load-elongation curve. The units are Joules (S.I.).
- Work = force x displacement (load x elongation)
-
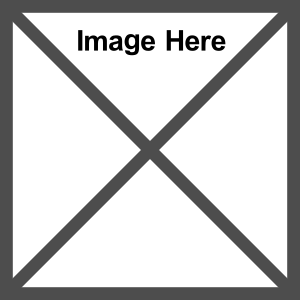
Stress strain curve for a relatively stiff and brittle fiber (A) and a relatively soft and tough fiber (B) having the same breaking stress
Rupture of work=?
Which fiber is tougher?
Breaking strength relationship?
Breaking elongation relationship?
Which is stiffer?
- Rupture of work: B > A
- Fiber B is tougher than fiber A
- Breaking strength: B = A
- Breaking elongation: B > A
- Fiber A is stiffer than fiber B
-
Initial (Young's) Modulus
- the slope of the tensile stress-strain curve at origin.
- Initial Modulus = Stress / Strain
- ~ Degree of elasticity or Stiffness
- The initial part of the curve is fairly straight, and its slope (ratio of stress to strain) usually remains constant.
- The modulus is measured in units of specific stress
- Modulus gives a measure of the force required to produce a small extension.
- An easily extensible/stretchable yarn will have low modulus.
- The reciprocal of modulus is called compliance.
- Modulus does not tell us any thing about the stiffness of yarn
-
Elastic Recovery
- The property of a body by virtue of which it tends to recover its original length/size/shape after deformation when the external load is removed
- Elastic recovery (%) = (elastic elongation / total elongation) x 100
-
Tensile testing machines
- We can increase the load attached to the specimen at constant rate and measure the corresponding elongation.
- We can extend the specimen at constant rate and measure the corresponding increase in the in building stress/tension.
- Depending upon these two principles we have namely three types of machines:
- CRL (constant rate of loading) and CRE (constant rate of elongation)
-
Constant rate of loading (tensile testing machine)
Specimen is attached between two jaws (grippers) J1, J2. consider J1 is fixed. In CRL the force applied to J2 jaw is increased at constant rate and corresponding elongation is measured.
-
Constant rate of elongation (tensile testing machine)
- In this case the jaw J2 is moved downward/upward at a constant rate or speed and corresponding increase in stress or tension is measured.
- The machine in the lab is CRE (Instron) the velocity of moving jaw is set to 10 inch/min
-
The effect of specimen length in CRE machine (tensile testing)
- Gauge length: distance between the edges of two jaws at the start of the test.
- If the specimen length in a CRE machine is increased, the rate of loading will decrease i.e. it will take longer to break.
-
Factors affecting tensile strength
- Raw material characteristics
- Yarn structure: irregularity, twist factor, etc.
- Fabric structure: setting, weave
- Fabric finish
-
Grab test (tensile test)
- Specimen=6" long and 4" wide
- Gage length=as 3 inch (75 cm).
- Clamp=1' wide.
-
"Fabric assistance" (strip test-tensile test)
- Consider the ratio: strip strength per thread / single thread strength
- The result is usually higher than unity.
- This indicates that the traverse threads have some form of binding effect on the longitudinal threads, so increasing their strength.
-
Strip test (tensile test)
- Fabric=1" wide
- Unravel yarns from sample to make clamp 1/2" wider than the fabric
-
Is it correct to compare the results of A (strip test) and B (grab test) directly? (Tensile test)
- If we calculate the ratio: grab strength / (strip strength / inch)
- The result is usually in the range of 1.0 to 2.0
- This indicates that the stressed zone of fabric between the jaws will be reinforced a little by the fabric on either side
-
BURSTING STRENGTH
The ability to retain physical integrity when subjected to a distending or swelling force, a force applied perpendicular to the fabric surface.
-
Hydraulic bursting strength tester
The fabric is clamped over a rubbery diaphragm that is expanded by fluid pressure.
-
TEAR STRENGTH
- The ability to resist rupture when a lateral (sideways) pulling force is applied.
- The force required either to start or to propagate a tear in a fabric under specified conditions.
-
Tearing
a progressive rupture along a line
-
Tear strength is high in a fabric if yarns...
- can group together under tearing force
- Grouping of yarns is made easier if the yarns are smooth and can slip over each other (yarn mobility)
-
Yarn mobility
- The ability of yarns in a fabric to shift, slide or move under a load.
- Yarn mobility increases when number of interlacing points (plain weave>twill), thread count, and yarn size all decrease
- Low yarn mobility -> one yarn breaks at a time, and the tearing strength approaches the single yarn strength.
-
Factors affecting tear strength
- Yarn strength
- Thread count
- Fabric structure (plain < twill < satin)
-
Tear strength tests
- Elmendorf Tear Strength test (Elmendorf tear strength tester)
- Tongue Tear Strength test (universal testing machine)
- Trapezoid Tear Strength test
-
Load-Elongation curve (tear strength)
- Elongation is given at constant rate (CRE) as the moving jaw moves at constant rate (10" per min)
- Corresponding change in the tension in the specimen is measured.
-
Abrasion
wearing away of any part of a material by rubbing against another surface.
-
Causes of abrasion in textiles
- Friction between Fabric and Fabric surfaces.
- Friction between Fabric and external surfaces.
- Friction between Fibers and dust or grit in a fabric that results in cutting of fibers.
-
Types of abrasion
- Flat abrasion
- Flex abrasion
- Edge abrasion
-
Assessment of abrasion damage
- Appearance against an un-abraded specimen
- The # of cycles required to produce a hole, broken threads, or broken strip.
- Loss in weight, often plotted against the # of cycles.
- Change in thickness (pile height, carpets).
- Loss in strength, e.g. tensile, bursting, tearing. Often expressed as a percentage of un-abraded strength.
- Change in other properties, e.g. air permeability, luster, color.
- Microscopic examination of damage to yarns and fibers.
-
Factors affecting abrasion resistance
- Fiber (mechanical properties, fiber shape)
- Yarn (yarn twist and size)
- Fabric structure (thickness, thread count, weave type)
-
Flat abrasion test measurement machine
- Rotary platform, double head
- Abrasion measurement on Taber tester
-
Drape coefficient measurement using Drapemeter formula
- Drape coefficient = (Area of fabric shadow / total fabric area) x 100
- Drape coefficient = (Weight of shadowed ring / total weight of ring) x 100
|
|