-
describe a typical stress-strain curve from tensile test on ductile metal, and physical processes which correspond to different parts on the curve
-
describe the difference between tresca and von mises yield criteria.
waht are the underlying physical principles of each criterion
- Tresca - yielding occurs when max shear stress on any plane reaches critical value. for metals, physical yielding mechanism is slip of crystal planes - shear deformation controlled by shear stress
- Von Mises - driving force for yield is strain energy associated with deviatoric components of stress tensor (shear strain energy). Failure occurs when distortion energy equals that at yield at uniaxial tension
-
critical stress intensity factor depends on sample thickness. why does this happen, and how does it influence fracture toughness testing procedure?
- Thin components (plane stress) - stress in thickness direction=0, poisson contraction in thickness direction occurs freely around crack tip. final fracture in plane stress usually preceded by considerable slow-stable crack growth.
- Thick components - strain in thickness direction limited, reducing plastic zone size. here fracture occurs suddenly with little crack growth
- Therefore fracture toughness under plane strain reaches it's minimum and better represents material property
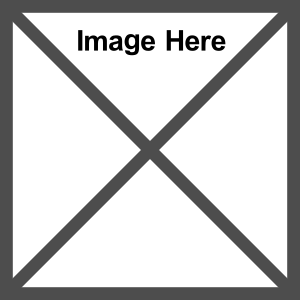
-
difference between stress concentration factor and stress intensity factor
- Both are derived from elastic theory
- One can often be derived from the other
- Concentration is a ratio of applied stress to local stress
- Intensity accounts for geometry, load and crack length and is not dimensionless (units MPa√m)
-
explain why failure stress of brittle materials is less than theoretical tensile strength
how can volume dependence of strength be explained (why bigger fail at lower stress than small)?
- brittle materials are defect sensitive, fail by fast fracture from defects well before yield.
- behaviour can be described by weakest link principle - an object is only as strong as its weakest part. i.e. macro-fracture initiation from one material element causes whole structure to fail
- brittle - failure dominated by flaws and cracks, these are statistically distributed, as is failure.
- larger samples are more likely to contain flaws and cracks than smaller samples therefore average strength of smaller sample is higher.
-
why is yield strength of materials several orders of magnitude less than theoretical
what's the physical mechanism of plastic deformation
- theoretical - shear strength = shear stress required to move one plane if atoms over another.
- real slip mechanism based on dislocation movements. involves displacement of only a few atoms at a time.
- therefore shear stress is a fraction of theoretical
-
describe leak-before-break criterion for pressure vehicles
in thin-walled pressure vessel with crack growing in wall, 2 possibilities
- 1 crack gradually penetrates wall, causing leak before sudden brittle failure occurs
- 2 sudden brittle failure occurs prior to vessel leaking
leak more preferable and easily detected from pressure drop from escape of vessel content
-
describe
a) stress concentration factor
b) fracture toughness
- a) goemetric discontinuities causeobjects to experience local increase in stress. scf is ratio of highest stress (sigma max) to a nominal stress (stress on net section)
- b) stress concentration is characterised by stress intensity factor K_I. critical value of SIF at which brittle failure occurs is fracture toughness
-
describe process of plastic deformation in polycrystalline materials.
are polycrystalline metals stronger than single-crystal equivalents?
give physical explanation for expected differences
- early yielding (and hardening) of well orientated grain
- additional yielding of less well orientated grains
- eventually all grains reach critical shear stress and full plasticity occurs
- polycrystalline metal stronger, means greater stresses required to initiate slip for yielding
-
describe how stress-strain curve for concrete differs between tension and compression. give physical explanation for expected differences.
- concrete compressive strength > tensile
- brittle tensile behaviour determined by micro cracks that grow and combine to cause failure
- if dominant stresses are compressive, cracks tend to have opposite sides pressed together so much less effect on material behaviour
-
explain which failure theory is most accurate in predicting yield of a ductile material:
max normal stress
max shear stress
max distortion energy
fracture mechanics stress intensity factor
-
describe following concepts
a) crack-tip singularity
b) stress intensity factor
- a) according to linear theory of elasticity, stresses near crack tip are
, where r is distance to crack tip. this means as r to zero, stress to infinity, therefore singularity exists at tip. Impossible in real materials, so region of yielding formed near tip (plastic zone) - magnitude of stress near crack tip characterised by stress intensity factor K_I:
fracture toughness i critical value of this at which fast brittle fracture occurs
-
describe possible strenghtening mechanisms in metals
what is fundamental physical basis for all these
plastic deformation is due to motionof large number of dislocations. ability of metal to plastically deform depends on ability of dislocations to move. so by reducing dislocation movement, mechanical strength can be improved
- grain size reduction - grain boundaries are barriers to dislocation movement. smaller grain size = more barriers
- solid solution alloying - impurity atoms distort lattice and generate stress. can be a barrier to dislocation motion
- strain hardening (cold working) - dislocation density increases. its motion becomes more difficult, making material stronger overall
-
differences between states of plane strain and plane stress
- plane strain - one component of strain tensor=0 (thick material)
- plane stress - one component of stress tensor = 0 (thin plate)
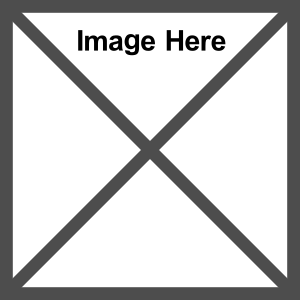
-
what's the difference between Linear elastic and elastic-plastic fracture mechanics?
- LEFM - considers linear dependencies of stress-strain
- EPFM - extends to elastic-plastic deformations of a body
Plastic deformation occurs in the area where stress exceeds the yield strength. Therefore, a plastic zone, whose size depends on the ratio 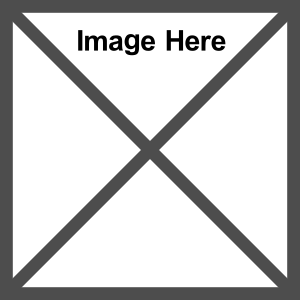 , occurs at the crack tip. If size of a plastic zone is small compared to the crack size and other geometrical parameters, then there will be a region outside of it where LEFM still applies, called the region of K-dominance, or the K-field. In this case the linear fracture mechanics gives a good approximation.
-
what's the importance of a plastic zone for material resistance to brittle fracture
crack growth requires energy, comes from stored elastic strain energy around crack, and is released as crack grows. During crack propagation, this energy is dissipated at crack tip (includes plastic dissipation and surface energy)
for large plastic zone, more energy needed for crack propagation - so material resistance to brittle fracture increases.
-
sketch a plot of growth rate da/dN against stress intensity range deltaK.
describe different regions of behaviour that may be seen
-
describe the difference between
a) engineering stress and true stress
b)engineering strain and true strain
- a) true stress = load/current cross sectional area. eng stress = load/original cross section
- b) true strain is calculated as a summation of small engineering strain increments
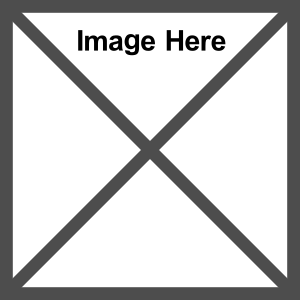
-
failure of brittle materials is often evaluated using probability methods
a)why are these well suited to failure in ideally brittle materials like glasses/ceramics
b)contrast such materials with composites which often prove unsuited to such methods
- ideally brittle materials fail by fast fracture from defects before yield. behaviour can be decsribed by weakest link hypothesis. flaws and cracks leading to failure are statistically distributed, so failure is too.
- composites don't satisfy weakest link assumption - failure of one part does not cause whole part to fail
|
|