-
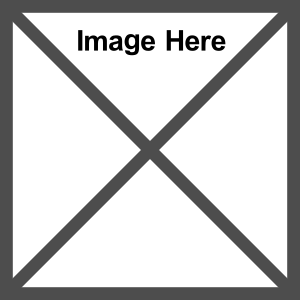
What is indicated by #1?
Illuminated (amber) – Hydraulic fluid used to cool and lubricate the corresponding electric motor driven pump has overheated or the pump itself has overheated.
-
What is indicated by #2?
Illuminated (amber) – output pressure of associated pump is low.
Note: When an engine fire switch is pulled, the low pressure light is deactivated
-
How can the engine driven pump LOW PRESSURE light be deactivated?
Pull the associated fire handle
-
How can the electric pump LOW PRESSURE light be deactivated?
Turn the associated switch off
-
What happens when you turn off an engine driven pump switch?
Output pressure is blocked by a blocking solenoid
-
What happens when you turn off an engine pump switch?
Shuts off fluid to the pump and and deactivates the LOW PRESSURE light
-
What is the normal hydraulic pressure?
3000 psi
-
What is the maximum hydraulic system pressure?
3500 psi
-
What is the minimum hydraulic system pressure?
2800 psi
-
What does and RF mean adjacent to the hydraulic quantity gauge?
Refill
-
When does an RF illuminate?
Hydraulic quantity below 76%
-
How does the output of an electric pump compare with the engine driven pump?
Engine driven pump is about six times the output of the electric pumps
-
Where are the heat exchangers for the hydraulic fluid?
The heat exchanger for system A is located in the main fuel tank No.1 and for system B is in the main fuel tank No.2
-
How much fuel is required in the main fuel tanks for ground operation of the electric pumps?
1675 lbs.
-
What are the consequences of a system A hydraulic leak in the engine pump or lines?
Fluid leaks to the standpipe (approximately 20% left at the standpipe)
-
System A-With fluid level at the top of the standpipe, the reservoir quantity displayed indicates approximately ___% full.
20%
-
What are the consequences if a leak develops in the system A or B electric motor drive pump?
Complete fluid loss, quantity will decrease to zero and all pressure is lost
-
What are the consequences of a leak in system B engine driven pump?
Fluid loss to standpipe (still allows PTU operation). Quantity will decrease to zero.
-
What are the consequences of a leak in the STBY system?
Complete fluid loss (B system leaks to 72%)
-
What is the purpose of the standpipe?
It supplies fluid to both the engine driven pump and electric motor driven pump and is sufficient for power transfer unit operation.
-
What does the PTU do?
It supplies the additional volume of hydraulic fluid needed to operate the autoslats and leading edge flaps and slats at the normal rate when system B engine-driven hydraulic pump is inoperative.
-
When does the PTU operate?
Airborne, flaps less than 15 but not up, and loss of system B engine driven pump pressure
-
What does the LGTU do?
The purpose of the LGTU is to supply the volume of hydraulic fluid needed to raise the landing gear at the normal rate when system A engine-driven pump volume is lost. The system B engine-driven pump supplies the volume of hydraulic fluid needed to operate the LGTU.
-
When does the LGTU operate?
Airborne, No. 1 engine RPM drops below limit value, landing gear lever is positioned UP, either main landing gear is not up and locked
-
The B system and the standby system share fluid. Will a leak in system B affect operation of the standby hydraulic system?
No
-
If there is a leak in the STBY system, will system B be affected?
No. Fluid level will stabilize at 72%
-
What does the STBY hydraulic system power?
Standby rudder, thrust reversers, leading edge flaps and slats (extend only), standby yaw damper
-
How is the STBY hydraulic system activated manually?
Either flight control switch to STBY RUD or ALTERNATE FLAPS master switch to ARM
-
How is the STBY HYD system activated automatically?
Loss of system A or B, flaps not up, 60 kts or greater or airborne OR the main PCU Force Fight Monitor (FFM) trips
-
Components of the A hydraulic system
A utopilot A
Rudder
E levator/elevator feel
A ileron
L anding gear
T hrust reverser 1
A lternate brakes
N osewheel steering
P TU
I B flight spoilers (1st and 3rd)
G round spoilers
-
Components of the B hydraulic system
A utopilot B
R udder
E levator/elevator feel
A ileron
L GTU
F laps (trailing edge)
L eading edge devices (flaps and slats)
A lternate nosewheel steering
A uto slats
T /R 2
B rakes
O utboard spoilers
Y aw damper
-
How are the hydraulic reservoirs pressurized?
System A and B reservoirs are pressurized by bleed air. The standby system reservoir is connected to the system B reservoir for pressurization and servicing.
|
|