-
Throughput
Rate at which system generates money through sales
-
Continuous Flow Mfg. (CFM)
- 1. One piece flow at a rate determined by the customer
- 2. Smooth and un-interrupted flow
-
Poka-Yoke
Eliminating possible errors; forgetfulness, misunderstanding, identification, willful errors, lack of standards, indadvertant errors.
-
Kanban-Pull
- 1. A method of material control.
- 2. A kanban card will give permission for the next operation to produce more parts.
-
Multi-Vari Analysis
- Chart to track variables like pr., temp, thk, customer complaints, etc at varying intervals.
- Variations within piece, piece-to-piece and time-to-time can be spotted.
- USL-Aim-LSL..
-
Seven Classical Wastes (MUDA)
- 1. Overproduction
- 2. Inventory
- 3. Rework/Rejects
- 4. Motion
- 5. Processing
- 6. Waiting
- 7. Transport
-
Andon Board
- 1. Visual control device - shows current state of production, indicates problems, etc
- Green - No problems
- Yellow - Situation needs assistance
- Red - Pdn. stopped
-
5S
- 1. Seiri - Sort
- 2. Seiton - Set in order
- 3. Seiso - Shine
- 4. Seiketsu - Standardize
- 5. Shitsuke - Sustain
-
Affinity Diagram
- Tool to organize complex info. into logical categories
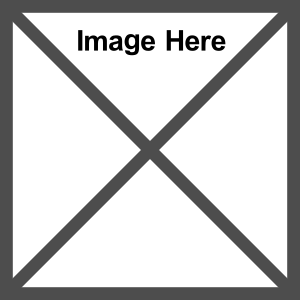
-
A3 Reports
- Concise summary of a project on a single sheet of paper
- 1. Uses concise wordings
- 2. Uses charts to illustrate points
- 3. Restricts to 3-4 bullets per section
- 4. Provides substance, not fluff.
-
Business Case
- A short summary of the strategic reasons for the project.
- 1. Design of a new project/process
- 2. Redesign of existing projects/process
-
Project Charter - Uses
- Team is aware of the project goals and boundaries
- Team will remain focussed on goals
- Team will work in alignment with the organization's goals
- Team champion will support the team and their goals
-
Spagetti Diagram
- Describing the flow of people, information or material in almost any type of process.
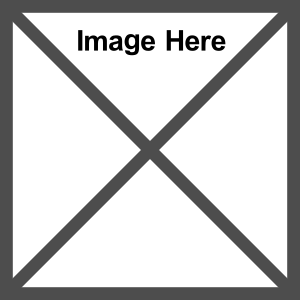
-
Pull Value (Value of the Pull System)
- 1. Cycle time reduction
- 2. Reduction in finished inventory
- 3. Reduction in WIP
- 4. Order stabilization by customers
- 5. Pricing stabilization
-
Kano Model/Analysis
- 1. Dissatisfiers (Basic reqmts., "must be")
- 2. Satisfiers (variable reqmts., "more is better")
- 3. Delighters (latent reqmts.)
-
Critical To Quality (CTQ) tree
- Focuses on key metrics of customer satisfaction
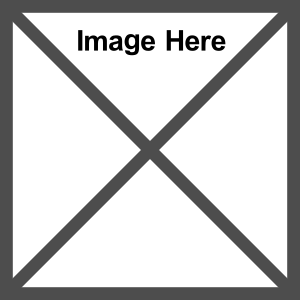
-
Voice of Customer (VOC)
- Enables the organization to:
- 1. Make decisions on products and services
- 2. Identify product features and specs.
- 3. Focus on improvmenet plans
- 4. Develop baseline metrics
- 5. Identify customer satisfaction drivers
-
Pareto Diagram
- Prioritize problems based on their frequency of occurance
- "Vital Few" and "Trivial Many"
- 20% 80%
-
-
Process Capability Studies
(Results)
- 1. Do Nothing: Process limits within spec. limits
- 2. Change Spec: If customer agrees
- 3. Center the process: If process spread matches spec. spread, but with a shift
- 4. Reduce Variability: DOE used to find variations
- 5. Accept the losses: Handle scrap and rework efficiently
-
Histogram
- Frequency column graphs displaying a static picture of process behavior
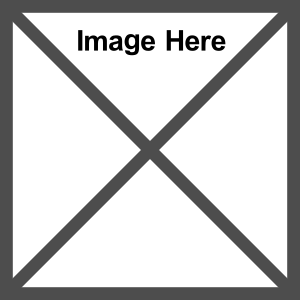
-
Sensitivity
Measure of the smallest change in measurand that can be sensed by the msmt. device
-
Resolution
Smallest msmt. change that can be represented by the display of the msmt. device
-
Repeatability
- 1. Measure of the ability of the msmt. process to repeatedly get the same results keeping all factors same.
- 2. Same gage and same operator
-
Precision
- 1. Repeatability and reproducibility
- 2. Describes how close successive msmt. results fall when repeated.
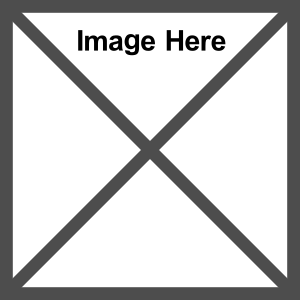
-
Reproducibility
- 1. Measure of ability of msmt. process to obtain same results under varying conditions.
- 2. Same gage, different operators - gage reproducibility
-
Bias/Offset
Systematic difference between 2 successive msmts. of the same thing
-
Accuracy
- 1. Degree of closeness of a msmt. to its true value
- 2. Lack of bias
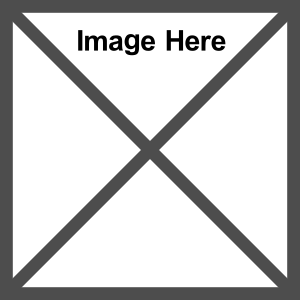
-
Data Coding
- 1. Too many digits of the measured value
- 2. Insensitivity due to rounding offs
- 3. Errors due to entering of large sequence of data by operators. So:
- Code: Xc = X + C, Decode: X1=Xc1- C and sigma = sigmac
Xc = X/f, Decode: X1 = Xc f and sigma = f x sigmac
-
Measles/Concentration Charts
- 1. Charts that utilize location data
- 2. To answer the question 'where'.
-
Takt Time
- Takt Time = Available pdn. time / Rate of customer demand
- It is the beat/rythm of the process.
|
|