-
Throughput
Rate at which system generates money through sales
-
Continuous Flow Mfg. (CFM)
- 1. One piece flow at a rate determined by the customer
- 2. Smooth and un-interrupted flow
-
Poka-Yoke
Eliminating possible errors; forgetfulness, misunderstanding, identification, willful errors, lack of standards, indadvertant errors.
-
Kanban-Pull
- 1. A method of material control.
- 2. A kanban card will give permission for the next operation to produce more parts.
-
Multi-Vari Analysis
- Chart to track variables like pr., temp, thk, customer complaints, etc at varying intervals.
- Variations within piece, piece-to-piece and time-to-time can be spotted.
- USL-Aim-LSL..
-
Seven Classical Wastes (MUDA)
- 1. Overproduction
- 2. Inventory
- 3. Rework/Rejects
- 4. Motion
- 5. Processing
- 6. Waiting
- 7. Transport
-
Andon Board
- 1. Visual control device - shows current state of production, indicates problems, etc
- Green - No problems
- Yellow - Situation needs assistance
- Red - Pdn. stopped
-
5S
- 1. Seiri - Sort - Get rid of what's not needed. (How often you use it?)
- 2. Seiton - Set in order - Organize, put in order and make things easy to find and use.
- 3. Seiso - Shine - Clean, repair and fix.
- 4. Seiketsu - Standardize - Standardize the new orderliness (checklists, photos, videos, etc)
- 5. Shitsuke - Sustain - Discipline to follow the new stds.
-
Affinity Diagram
- Tool to organize complex info. into logical categories
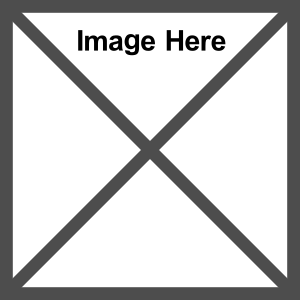
-
A3 Reports
- Concise summary of a project on a single sheet of paper
- 1. Uses concise wordings
- 2. Uses charts to illustrate points
- 3. Restricts to 3-4 bullets per section
- 4. Provides substance, not fluff.
-
Business Case
- A short summary of the strategic reasons for the project.
- 1. Design of a new project/process
- 2. Redesign of existing projects/process
-
Project Charter - Uses
- Team is aware of the project goals and boundaries
- Team will remain focussed on goals
- Team will work in alignment with the organization's goals
- Team champion will support the team and their goals
-
Spagetti Diagram
- Describing the flow of people, information or material in almost any type of process.
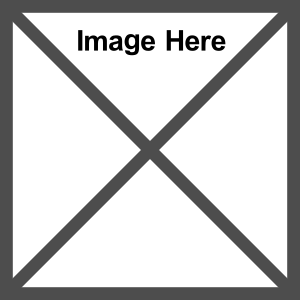
-
Pull Value (Value of the Pull System)
- 1. Cycle time reduction
- 2. Reduction in finished inventory
- 3. Reduction in WIP
- 4. Order stabilization by customers
- 5. Pricing stabilization
-
Kano Model/Analysis
- 1. Dissatisfiers (Basic reqmts., "must be")
- 2. Satisfiers (variable reqmts., "more is better")
- 3. Delighters (latent reqmts.)
-
Critical To Quality (CTQ) tree
- Focuses on key metrics of customer satisfaction
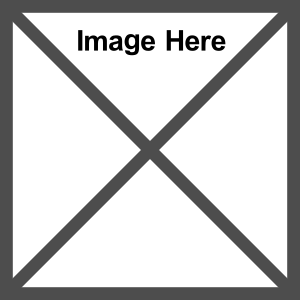
-
Voice of Customer (VOC)
- Enables the organization to:
- 1. Make decisions on products and services
- 2. Identify product features and specs.
- 3. Focus on improvmenet plans
- 4. Develop baseline metrics
- 5. Identify customer satisfaction drivers
-
Pareto Diagram
- Prioritize problems based on their frequency of occurance
- "Vital Few" and "Trivial Many"
- 20% 80%
-
-
Process Capability Studies
(Results)
- 1. Do Nothing: Process limits within spec. limits
- 2. Change Spec: If customer agrees
- 3. Center the process: If process spread matches spec. spread, but with a shift
- 4. Reduce Variability: DOE used to find variations
- 5. Accept the losses: Handle scrap and rework efficiently
-
Histogram
- Bar graphs giving the distribution of data, used to find mean, median, std. deviation, etc.
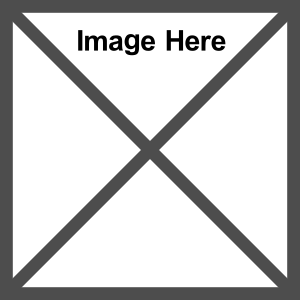
-
Sensitivity
Measure of the smallest change in measurand that can be sensed by the msmt. device
-
Resolution
Smallest msmt. change that can be represented by the display of the msmt. device
-
Repeatability
- 1. Measure of the ability of the msmt. process to repeatedly get the same results keeping all factors same.
- 2. Same gage and same operator
-
Precision
- 1. Repeatability and reproducibility
- 2. Describes how close successive msmt. results fall when repeated.
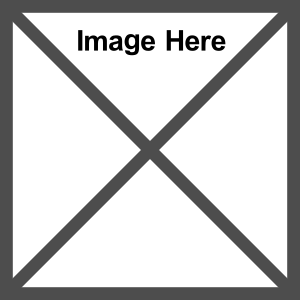
-
Reproducibility
- 1. Measure of ability of msmt. process to obtain same results under varying conditions.
- 2. Same gage, different operators - gage reproducibility
-
Bias/Offset
Systematic difference between 2 successive msmts. of the same thing
-
Accuracy
- 1. Degree of closeness of a msmt. to its true value
- 2. Lack of bias
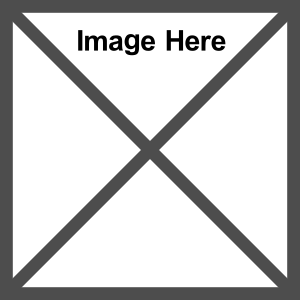
-
Data Coding
- 1. Too many digits of the measured value
- 2. Insensitivity due to rounding offs
- 3. Errors due to entering of large sequence of data by operators. So:
- Code: Xc = X + C, Decode: X1=Xc1- C and sigma = sigmac
-
Xc = X/f, Decode: X1 = Xc f and sigma = f x sigmac
-
Measles/Concentration Charts
- 1. Charts that utilize location data
- 2. To answer the question 'where'.
-
Takt Time
- Takt Time = Available pdn. time / Rate of customer demand
- It is the beat/rythm of the process.
-
Six Sigma
A business mgmt. strategy that seeks to improve the quality of process outputs by identifying and removing the causes of errors and variablilty in the processes.
-
DMAIC
Define-Measure-Analyze-Improve-Control
-
DMADV
Define-Measure-Analyze-Design-Verify
-
6σ (Meaning)
- If one has 6 std. deviations b/w the process mean and the nearest spec. limit, practically no item fails to meet specs. At the max. such a process can have 3.4 defects per million in the long run.
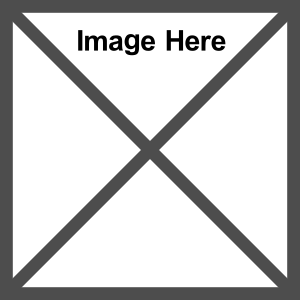
-
5 Whys
- Root Cause Analysis:
- Car not starting - Battery Dead - Alternator not working - Belt Broken - Old - No Maintenance
-
Process Capability
Tells whether the process is capable of meeting the specs or not. Statistical methods are used to find the mean and std. deviation of the data histogram.
-
ANOVA
Analysis of Variance - tells whether the means of two or more groups of data are equal or not.
-
Gage R&R
Measure of repeatability and reproducability of msmt.
-
Regression
Helps in understanding how the value of the dependent variable changes with variation of any one of the independent variables, while maintaining all others fixed.
-
Correlation
- Indicates the strength and direction of a relationship b/w two random variables.
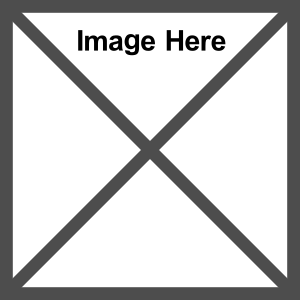
-
FMEA
Analysis of the potential failures within a system for classification by severity.
-
Contingency Tables
- Tables used to record and analyze the relationship b/w two or more 'categorical' variables.
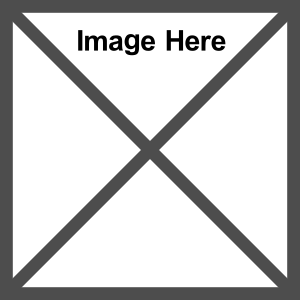
-
Non-parametric Methods
- Methods used to conduct hypothesis tests of means of 'non-normal' data.
- These methods are based on 'Rank Ordering' of the response.
- Softwares to conducts such tests are: Wilcoxon Sign Ranked test, etc
-
Sample Size Selection
Deciding on the number of data samples to be tested to have the results of the statistical analysis within a given confidence interval.
-
DOE
Conducting experiments to decide on the relationship b/w a dependent variable and independent variables by having various levels of the independent variables (factors) and monitoring the response of the system.
-
-
Push System
- Initiates pdn. in response to 'anticipated demand'
- It is a "ready or not, here I come" system. Ex: McDonalds
-
Pull System
- Initiates demand in response to 'present demand'.
- It is a "don't call me, I'll call you" system. Ex: Wendy's
-
Set-up Time
The time b/w the 'last good piece' from the previous pdn. run and the 'first good piece' from the new pdn. run.
-
Six Shopfloor Losses
- 1. Breakdowns
- 2. Set-ups and adjustments
- 3. Idling and minor stoppages
- 4. Reduced speeds
- 5. Quality defects and reworks
- 6. Startup losses
-
5 Elements of Pdn
- 1. Objects of pdn. - the products
- 2. Agents of pdn. - the people making the products; tools, etc
- 3. Methods - means by which actions are performed
- 4. Space - where action is performed
- 5. Time - how long action takes for completion
-
Pacemaker Process
- In supermarket pull systems, customer schedule is sent to only one pdn. process in the door-to-door value stream. This process is called the pacemaker process.
-
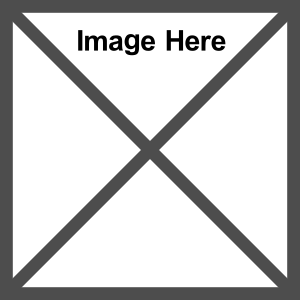
-
Supermarket
- When continuous flow is not possible due to very fast or very slow processes or other logistics issues, then a supermarket pull system is used to eliminate the need to schedule production for the processes that are not linked.
- Simply put, SM is the installation of a pull system where continuous flow is interrupted and the upstream process must still operate in a batch mode.
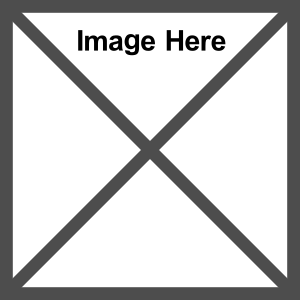
-
Pitch (VSM term)
Pitch time might be the time to produce the amount of material typically moved at one time, like one skid of material.
-
8D Problem Solving Technique
- Structured method emphasizing team synergy. "The team as a whole is better and smarter than the quality sum of the individuals.
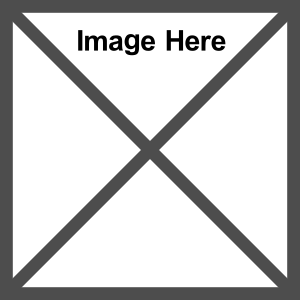
-
1 Sample T Test
- a) Used to determine whether a population mean (u) is equal to a hypothesized value.
- b) Used with continuous data from a single random sample, normally distributed.
-
Confidence Interval
- CI is a range of likely values for a population parameter (say u) that is based on the sample data.
- CI quantifies the precision of the estimate.
-
Power Analysis
- Power is the ability of a test to detect a difference when one exists (Probability of rejecting Ho when its false)
- PA would answer one of these questions:
- How many samples are needed?
- Is the sample size good enough?
- How large a difference can be detected by the test?
- Are the results trustworthy?
-
2 Sample T Test
- Used to determine whether there is a statistical difference between two population means.
- Continuous data from 2 independent samples
- Seperate normality tests for each.
-
Paired T Test
- Used to determine whether there is a statistical difference b/w two paired populations.
- One element in common b/w samples
- Normality test for diff. b/w samples.
-
1-Proportion Test
- Used to see what proportion of the population has defects.
- This test determines whether adequate evidence exists that the proportion of events (defects, etc) is different from a hypothesized value.
NOTE: Success/Reject data (as opposed to continuous msmts.). do not capture detailed info about the sampled parts, sample sizes are commonly large.
-
2 Proportions Test
A test of two proportions determines whether sufficient evidence exists that two proportions are different from one another.
-
Correlation
helps to compare two independent msmt systems so that we can eliminate either one if there is a sound correlation.
-
Simple Regression
- Helps in knowing how important is X in predicting Y.
- How would Y vary with X?
-
One Way Anova Test
- Generalization of a 2 sample T test.
- However, more than 2 groups of samples can be analyzed.
- Comparing means and variances between sample groups.
|
|