-
What is Forecasting?
- A combination of the art and science of predicting future events.
- -Art: managerial judgement
- -Science: sophisticated mathematical tools & methods
-
What is a forecast?
- An inference of what is likely to happen in the future. Provides a basis for coordination of the plans of various functions.
- -finance: amount of capital
- -personnel: size and mix of workforce
- -purchasing: proper materials
-
Types of Forecasts?
- 1. Technological
- 2. Economic
- 3. Demand
-
When to use Qualitative Forecasting Methods?
- 1. When data is not available
- 2. When data is not representative of the future (new products/techology)
-
Qualitative Forecasting Approaches?
- 1. Jury of Executive opinion
- 2. Sales Force
- 3. Delphi Method
- 4. Consumer Market Survey
-
Describe Jury of Executivew Opinion
- A small group of managers in various functions may meet and collectively develop a forecast
- Advantage: Considerable knowledge & talent
- Risk: Bandwagon effect
- Ex: Bristol Myers Squibb/Cancer treatment
-
Describe Delphi Method
- Managers and staff complete a series of questionaires each developed from the previous one to achieve a consensus forecast.
- Advantage: Anonymity encourages honest responses, useful for remote participants, avoids bandwagon effect.
- Disadvantage: Lack of expertise, Ambiguity possible in questionaire, no accountability.
- Ex: Rand Corp/Atomic Bomb impact
-
Describe Sales Force Composite
- Sales persons estimate sdales in their respective regions, aggregated at the district and national levels.
- Advantage: Sales staff aware of customer plans, direct contact to customers
- Risk: Hard to distinguish between customer intentions and actuality, overly influenced by recent experiences.
-
Consumer Surveys
- Solicit input directly from a sample of customers
- Advantage: Tap information not available elsewhere
- Risk: Requires considerable knowledge and skill to handle surveys, expensive and time consuming, low response rates possible
-
Measures of Forecast Accuracy
- 1. Mean Forecast Error (MFE)
- 2. Mean Absolute Deviation (MAD)
- 3. Mean Squared Error (MSE)
- 4. Tracking Signal
-
Mean Forecast Error
MFE helps to determine if your method is biased or unbiased
-
Mean Absolute Deviation
MAD tells you the magnitude of how much you are off, the lower the better.
-
Mean Squared Error
The penalty exponentially increases for higher deviation.
-
Tracking Signal
Recalculates the cumulative errors, tracks bias AND magnitude
-
What type of Time Series Component does this graph represent?
Random Component (noise)
-
What type of Time Series Component is represented?
Trend Component
-
What type of Trend Series component is represented?
Cycle Component
-
What type of Time Series Component is represented?
Seasonal Componet
-
Three Forecasting Methods?
- 1) Simple Moving Average
- 2) Weighted Moving Average
- 3) Single Exponential Smoothing
-
Formula for Simple Single Exponential Smoothing?
-
When Alpha=close to zero?
Gives a stable forecast
-
When Alpha =close to one?
Responsive Forecast
-
When Alpha = 0?
- Ft+1=Ft
- Not Naive - same as last months forecast
-
When Alpha is 1?
- Ft+1=At
- Naive - same as last months actual
-
What is the Decision Variable and Desirable Characteristics of Simple Moving Average Forecasting method?
- N (number of periods)
- Stability = N Large
- Responsiveness = N Small
-
What is the Decision Variable and Desirable Characteristics of Weighted moving Average Forecasting Method?
- Weight for each Period, N
- Stability: Low Weight applied to recent period, N Large
- Responsiveness: High Weight to more recent period, N Small
-
Decision Variable and Desirable Characteristics for Single Exponential Smoothing Forecasting Method?
- Alpha
- Low Alpha = Stable
- High Alpha = Responsiveness
-
What is Capacity?
Maximum rate of output
-
List some measures of capacity?
- Output: Rates for different products
- Inputs: Machine hours available, seating capacity, # beds.
-
List the importance of Capacity Decisions?
- 1. Impacts ability to meet future demands
- 2. Affects operating costs (under/over capacity)
- 3. Major determinant of initial costs
- 4. Involved long-term commitment
- 5. Affects competitiveness (del speed/barrier to entry)
- 6. Affects ease of management (capacity =?demand)
-
Examples of fluctuating demand?
- Time of day>>Movies, Bowling alleys
- Days of week>>Repairing, Painting, U-Haul
- Times of the month>>Financial Services, Paydays
- Seasons of the year>>Roofing, income tax
-
Why is it easier to manage capacity and demand in manufacturing than services?
- 1. Processing time varies due to customer involvement
- 2. Intangible service Output (qualitative & subjective)
- 3. Time perishable capacity
- 4. Service can't be inventoried
-
How do you manage capacity and demand?
- Capacity: What type? (money, time, equipment, human, etc)
- How Much?
- When needed?
- Demand: Forecast
- Supply: Availability
-
Types of Capacity?
- Human
- -Number, Skills-Level and mix
- Facilities
- -Single/multiple, main/satellite
- Equipment
- -Computer system
- -Substitutions, modifications
- Tools
- -computerized notifications
- Money
- -credit card firms can carry limited receivables
- Time
- -Hrs/day, days/week service provided
- Alternative Sources
- -subcontract or lease resources
-
Two Strategies for managing capacity?
- 1. Lead Strategy (flexibility)
- -Build in idle capacity
- -Expand in anticipation of increase in demand
- (Economics of small increases vs. a large increase FP&L)
- 2. Lag Strategy (price)
- -Expand only after capacity has fallen below demand
-
Capacity increases in _____________?
Chunks or Increments
-
Define and Measure Capacity?
- Design Capacity: maximum obtainable output
- Effective Capacity: Max capacity given product mix, scheduling difficulties, and other doses of reality
- Actual output: rate of output actually achieved -cannot exceed effective capacity.
-
Efficiency ratio?
Efficiency = Actual Output / Effective Capacity
-
Utilization Ratio?
Utilization = Actual Outpu / Design Capacity
-
Yield Management with Efficiency Utilization
-
Developing Capacity Alternatives?
- Do nothing
- Design flexibility into systems
- Differentiate between new and mature products or services
- Take a big picture approach (motel rooms/parking)
- Prepare to deal with capacity chunks
- Smooth out capacity requirements
- Identify optimal operating levels
-
Drivers for Location Planning?
- 1. Viewed as a marketing/operations strategy
- 2. Growth in demand
- 3. Depletion of basic inputs
- 4. A shift in the market
- 5. Closts of doing business at a particular location
-
Why are location decisions so important?
They are long term committments with large costs.
-
What are the objectives of Location Decisions?
- 1. Profit Potential
- 2. Balance cost and customer service
-
What options are there for Location Decisions?
- 1. Expand existing facilities
- 2. Add new facilities
- 3. Move
-
Give two short-term reasons NOT to make a location decision?
- 1. wage rates
- 2. exchange rates
-
Best approach to location decision?
Consider how location impacts development of long-term capabilities.
-
Six Step Process for Location Decision?
- 1. Identify sources of value
- 2. Identify capabilities needed (for a competitive advantage)
- 3. Assess implications of location decision on development of capabilites (quality coils)
- 4. Identify potential locations
- 5. Evaluate locations
- 6. Develop strategy for building network of locations
-
Levels of location decisions?
- 1. Continent/Country
- 2. Region within a country
- 3. Community / Locality
- 4. Specific site
-
Factors affecting Regional & Country Level Decision?
- 1. Minimize transportation costs and provide acceptable service
- 2. Proper supply of labor
- 3. Wage rates
- 4. Unions
- 5. Regional taxes, regulations, trade barriers
- 6. Political stability
-
Factors affecting Community Level Location Decision?
- 1. Availability of acceptable sites
- 2. Local government attitudes
- 3. Regulations, zoning, taxes, labor supply
- 4. Tax incentives
- 5. Community's attitude
- 6. Amenities
-
Factors affecting Site Level Decision?
- 1. Size
- 2. Adjoining land
- 3. Zoning
- 4. Drainage
- 5. Soil
- 6. Availability of water, sewers, utilities
- 7. Development costs
-
List the considerations of manufacturing/distribution for location planning?
- 1. Cost focus
- 2. Transportation modes/costs
- 3. Energy availability costs
- 4. Labor cost/availability/skills
- 5. Building/leasing costs
-
List the considerations Service/Retail for location planning?
- 1. Revenue focus
- 2. Demographics, age, income, etc.
- 3. Population/drawing area
- 4. Competition
- 5. Traffic volume/patterns
- 6. Customer access/parking
-
Cost volume profit analysis in evaluating locations?
- 1. Determine fixed and variable costs
- 2. Plot total costs
- 3. Determine lowest total costs
-
Cost Volume Profit Analysis:
Lower volumes are best with lower _______Cost
Higher volumes are best wtih lower _________Cost
-
Three methods for evaluation Locations?
- 1. Transportation Model
- -Decision based on movement costs of raw materials of finished goods
- 2. Factor Rating (most popular)
- - Decision based on quantitative and qualitative inputs
- 3. Center of Gravity Method
- Decision based on minimum distribution costs
-
Using the Factor Rating Method for Location decisions, the best alternative is the one with?
Higher composit score
-
Factors that affect Process Selection?
- 1. Forecasting
- 2. Products & Service design
- 3. Technological change
- 4. Capacity planning
- 5. Facilities & Equipment
- 6. Layout
- 7. Work design
-
Factors to consider when deciding to make or buy components?
- 1. Available capacity
- 2. Expertise
- 3. Quality consideration
- 4. The nature of demand
- 5. Cost
-
List 5 Process types?
- 1. Job Shops (small runs)
- 2. Batch Processing
- 3. Repetitive/Assembly (semicontinuous)
- 4. Continuous Process
- 5. Projects (nonroutine jobs)
-
This process type is low volume, high variety, high flexibility?
Job Shop
-
This process is moderate volume, moderate variety, moderate flexibility?
Batch
-
This process is High Volume, Low Variety, Low Flexibility?
Repetitive Assembly
-
This process is very high volume, very low variety, very low flexibility?
Continuous Flow
-
Describe Job Shop?
Examples of Process?
Examples of Goods & Services?
Competitive Advantages?
- Customized good or services
- Machine Shop, Beauty Shop
- Specialty tools, Hair Styling
- Quality (performance) & Flexibilty
-
Describe Batch?
Examples of Process?
Examples of Goods & Services?
Competitive Advantages?
- Semi-standard goods or services
- Bakery, Classroom
- Cookies, education
- Moderate cost & flexibility
-
Describe Repetitive/Assembly?
Examples of Process?
Examples of Goods & Services?
Competitive Advantages?
- Standardized goods or services
- Assembly line, cafeteria line
- Automotive line, car wash
- Low unit cost, Dependability
-
Describe Continuous?
Examples of Process?
Examples of Goods & Services?
Competitive Advantages?
- Highly standardized goods or services
- Steel Mill, Sugar refinery
- Steel, Paper, Power
- Low Price, Quality (conformance)
-
Describe Layout?
Layout is the configuration of departments, work centers, and equipment, with particular emphasis on movement of work (customers or materials) through the system.
-
Three basic layout types?
- 1. Product Layouts
- 2. Process Layouts
- 3. Fixed-Position
-
Describe Product Layout and which processes use it?
- Product Layout uses standardized processing operation to achieve smooth, rapid, high volume flow.
- Line
-
Describe Process Layout and which processes use it?
- Process layout can handle varied processing requirements.
- Job Shop or Batch (ex: hospital)
-
Describe Fixed-Position Layout and process that uses it?
- Fixed Position is a layout in which the product or project remains stationary, and workers, materials, and equipment are moved as needed.
- Project! Ex: Building or freeway
-
Importance of Layout Decisions?
- 1. Requires substantial investments of money and effort
- 2. Involves long-term commitments
- 3. Has significant impact on cost and efficiency of short-term operations
-
Eight things that cause a need for layout decisions?
- 1. Inefficient operations
- 2. Changes in the design of products or services
- 3. The introduction of new products or services
- 4. Accidents/Safety hazards
- 5. Changes in environmental or other legal requirements
- 6. Changes in volume of output or mix of products
- 7. Changes in methods and equipment
- 8. Morale problems
-
Layout Formats?
- 1. Group Technology Layout
- 2. Just-In-Time Layouts
- -May be assembly-line or
- -Group Technology formats
- 3. Fixed Position Layout
- -eg Shipbuilding
-
Cellular Layouts include?
- 1. Cellular Manufacturing
- 2. Group Technology
- 3. Flexible Manufacturing Systems
-
The advantage of Cellular Layouts?
- They retain flexibility in the process and gain economies of scale.
- Ex: Lazyboy Case
-
Explain Cellular Manufacturing?
Layout in which machines are grouped into a cell that can process items that have similar processing requirements.
-
Explain Group Technology Layout?
The grouping into part families of items with similar design or manufacturing characteristics.
-
A Flow Line for Production or Service?
-
A U-Shaped Production Line looks like?
-
Adavantages of U-Shaped Production Line?
- 1. Shorter distance
- 2. Workers can alternate tasks
- 3. Shipping & Receiving can be in 1 place
-
Describe Process Layout?
- Departmentalized process where work travels to dedicated process centers
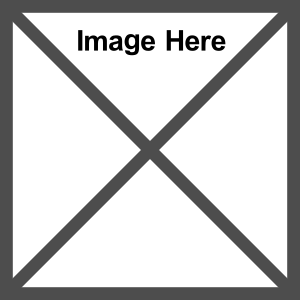
-
-
Cellular Manufacturing Layout?
- Part families are based on Group Technology
- -minimizes material movement
- -efficient, but still flexible
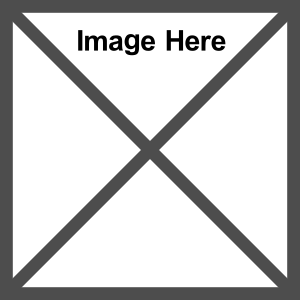
-
Line Balancing?
is the process of assigning tasks to workstations in such a way that the workstations have approximately equal time requirements.
-
Cycle Time?
is the maximum time allowed at each workstation to complete its set of tasks on a unit.
-
Determine maximum Output?
|
|