-
is defined as the resistance of a material to external elements such as force, load, or weight measured in pounds per square inch (PSI).
Stress
-
is the amount of deformation or stretch that occurs over a standard gage length (2") expressed in inches or a percentage.
Strain
-
Stress is equal to divided by .
- Applied force
- Cross-sectional area
-
Strain is equal to divided by .
- deformation
- original length
-
The four types of stress involved in strengths of materials are:
a. tension
b. compression
c. torsion
d. shear
-
The primary objective of the tensile test is to determine the a specimen can resist before taking a set or before occurs.
max load, permanent, rupture
-
materials will neck down through the plastic range before rupture occurs.
Ductile
-
materials do not neck down significantly; instead, they fail sharply and abruptly at the maximum load(because brittle materials do not exhibit much plasticity).
Brittle
-
Proportional Limit
the stress value at which the elastic portion of the curve loses it's proportionality between stress and strain
-
Yield Stress
the top of the elastic region, where the amount of strain increases with little increase in stress.
-
Tensile strength
maximum load divided by original area.
-
Percent Elongation
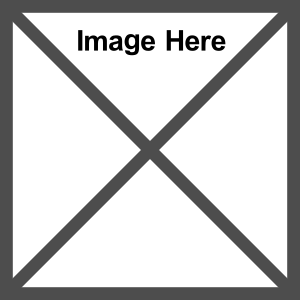 - Lf = length at fracture
- Lo = length original
-
Percent Reduction of Area
(Ao-Af/Ao)x100
Ao=Area of original cross section
Af=Area of final cross section
-
Modulus of Elasticity
is a measure of the ability of a material to withstand changes in length when under lengthwise tension or compression.
-
Ductility
the property that allows a material to deform permanently, under tension.
-
Malleability
the property that allows a material to deform permanently, in compression.
-
Plasticity
the ability of a metal to be deformed permanently, without failing.
-
Creep
The plastic deformation resulting from the application of a long-term load.
is a slow, but steadily increasing strain applied to a material under load.
is important in structures as bridges, buildings and other load-bearing structures in which the members are subjected to long-term static loads.
-
Hardness
is generally referred to as a material's property that indicates resistance to surface penetration.
may be either static or dynamic.
is measured by resistance to indentation.
-
Common static hardness tests:
Brinell
Rockwell
Vickers
-
The hardness test is the oldest and most established method.
Brinell
-
Rockwell Scales
B - for testing materials of medium hardness.
C - for testing very hard materials.
-
hardness testers are indentation tests and depend on the calculation of energy absorbed by the specimen during the test.
Dynamic
-
The general outcome of an impact test is the determination of the energy required to the specimen.
break
-
is an indication of how well a material can withstand shock loading.
Impact stregth
-
is used to measure the transfer of energy required to break a given volume of material.
Impact testing
-
Two common forms of impact testing are:
Izod
Charpy
-
is defined as the failure of a material due to repeated or cyclic stresses being applied to it.
Fatigue
-
is the stress at which a material fails by fatigue.
Fatigue strength
-
Three factors affecting fatigue are:
Temperature
Composition and structure of the material
Imperfections such as surface scratches, notches, inclusions, and other defects that can help initiate cracking.
-
NDT stands for
Non-Destructive Testing
-
NDT is typically used to identify defects such as , , or that might lead to the failure of the part.
voids, inclusions, cracks
-
Four types of NDT testing are:
magnetic particle
flourescent penetrant
x-ray
Ultrasonic
-
A is an applied force that acts in a direction parallel to the plane in which the force is applied.
shearing stress
-
Direct shearing occurs when parallel forces are applied in opposite directions.
Single-shear forces occur along a plane.
Double-shear forces occur between planes simultaneously.
single, two
-
When a material is bent or flexed under a load, a portion of the cross section is under and a portion is under .
tension, compression
-
Somewhere between these two opposing forces is a line, or axis, separating the forces. Along this axis, the specimen is in tension nor in compression.
neutral, neither
-
The of a beam is the displacement of a point on the neutral surface of a beam from its original position under the action of applied loads.
deflection
-
Compression
tends to compact or squeeze the specimen.
-
Torsion
uses a twisting motion to test the strength of the specimen.
-
Non-Destructive Testing
does not render the part unusable for its intended purpose.
-
Shear
applies force perpendicular to the primary axis of the part.
-
Hardness
measures the resistance to surface penetration.
-
Flexure
most commonly used to determine the cross-sectional geometry for a given application.
-
Fatigue
uses repeated, cyclic motions to determine the point of failure for a given part or specimen.
-
Creep
conducted over a very long period of time.
-
Tensile
tends to pull the specimen apart.
-
Impact
used to measure the transfer of energy required to break a specimen.
|
|