-
Warum ist die Erwähnung der Maß - und Formgenauigkeit bei Kunststoffteilen wichtig?
- Spritzgussteile erhalten ihre endgültige Gestalt bereits während des Urformprozesses (keine Nachbearbeitung)
- Schwindung und Verzug zu beachten
- nach Material und Gebrauchumgebung auch Quelldehnung
- für Kunststoffe nicht die selben Toleranzklassen wie für Metalle
-
Was ist Schwindung?
Schwindung als die Differenz zwischen den Maßen der kalten Form und den Maßen des Formteils nach sechzehnstündiger Lagerung im Normklima definiert.
-
Wodurch kann eine Schwindung von der linearen Schwindung abweichen (4)?
- Anisotropien im Werkstoff (bsp. Glasfasern)
- Schwindungsbehinderung durch Werkzeug (z.B. Kerne)
- Schwindungsbehinderung durch bereits erstarrte Randschichten
- Örtlich verschiedene Abkühlverhältnisse
-
Welche Arten der Schwindung werden unterschieden (5)?
- Thermische Schwindung
- Druckabhängige Schwindung
- Umwandlungsschwindung
- Reaktionsschwindung
- Schrumpfung
-
Was ist Thermische Schwindung?
Hervorgerufen durch Volumenänderung durch Temperaturänderung. Der häufigste Fall ist hier die Volumenverkleinerung während des Abkühlprozesses in der Urformphase.
-
Was ist Druckabhängige Schwindung?
Durch Absenken des Drucks dehnt sich das Formteil während der Urformphase aus.
-
Was ist Umwandlungsschwindung?
Induziert durch Kristallisation
-
Was ist Reaktionsschwindung?
hervorgerufen durch chemische Reaktionen während des Formgebungsprozesses
-
Was ist Schrumpfung?
Relaxationsschwindung von verarbeitungsbedingten Molekülorientierungen
-
Nenne die Schwindung in % einiger Kunststoffe!
Was ist generell zu beobachten?
- unterschiedlich starke Schwindung bei amorphen und kristallinen Kunststoffen
- Behinderung der Schwindung durch Füllstoffe
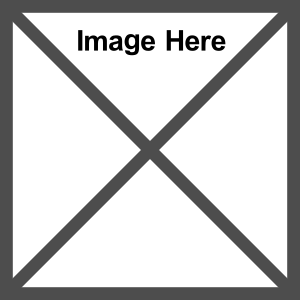
-
Trage das Formteilmaß eines gerade gefertigten Kunststoffteiles (z.B. Spritzgussteil) über der Zeit auf (qualitativ)!
-
Beschreibe die Punkte!
- Verarbeitung:
- 0: Maß des kalten Werkzeugs
- 1: Maß des aufgeheizten Werkzeugs
- 2: elast. Aufweitung des Werkzeugs durch Innendruck
- 3: Maß des Formteils nach dem Entformen
- Lagerung:
- 4: Messung der VS nach DIN 16901
- 6-7: Ausdehnung nach Aufheizen
- 7-8: NS durch Warmlagerung
- 8-9: Volumenverringerung durch Abkühlen
- Gebrauch:
- 5: Maß nach sehr langer Lagerzeit
- 5-10: Quelldehnung (z.B. Wasseraufnahme)
-
Was ist Nachkristallisation?
Wozu führt sie?
- Verbesserung des Kristallisationsgrades durch Ausheilung von Baufehlern in Kristallen oder Einbau freihängender Kettenreste
- Vorgang dauert sehr lang und ist kaum beschreibbar
- Änderung von Dichte, E-Modul, Schlagzähigkeit u.ä. von Kunststoff-Fertigteilen noch nach Monaten möglich (Relaxation)
- => führt zu Volumenschwindung
-
Trage das spezifische Volumen eines Kunstoffes über die Temperatur auf (schnelle und langsame Abkühlung)!
Kennzeichne die Nachkristallisation!
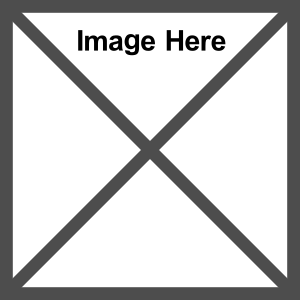 - => kann auch bei Temperaturen unter der Schmelztemp statfinden (z.B. im Betrieb)
-
Was siehst du?
Benne Punkte!
- pvT-Diagramm (Polystyrol)
- (1) Werkzeuginnendruck erreicht Atmosphärendruck
- (2) Entformung
- (3) Gebrauchspunkt
-
Nenne Einflussmöglichkeiten auf Schwindung (8)!
- Massetemperatur
- Werkzeugtemperatur
- Einspritzgeschwindigkeit
- Nachdruckhöhe
- Wirksame Nachdruckzeit
- Molekülorientierungen
- Orient. Längs. Füllstoffe
- Wanddicke
-
Zeige ob sich die jeweilige Einflussgröße verstärkend abschwächend oder gar nicht in jeweiliger Form auswirkt!
-
Zeige qualitativ wie sich ein glasfaserverstärkter Kunststoff im Bezug auf die Schwindung parallel und senkrecht zu den Fasern verhält.
Trage sowohl Nachdruck, Werkzeugtemperatur, als auch Einspritzzeit über der lokalen Schwindung auf!
-
Was ist Verzug?
Abweichung von der Sollgestalt eines Formteils. Verzug ist immer die Folge von Schwindungsunterschieden im Bauteil
-
Nenne Gründe für Verzug (3)!
- Werkstoffanisotropie
- Ortsvariabler Werkzeuginnendruck
- Ortsvariable Abkühlverhältnisse
-
Zeige wie eine Eigenspannungsverteilung zustande kommt!
(erst Temperaturverlauf, dann ohne mechanische Kopplung und mit mechanischer Kopplung)
-
Erkläre was du hier siehst!
- Platte mit dicken Rippen auf der Innenseite wird sich nach außen wölben und zusätzlich gegenüber den Rippen Einfallstellen bilden (links)
- Viele dünne Rippen bewirken das Gegenteil, bilden jedoch keine Einfallstellen aus (rechts)
-
Erkläre was du hier siehst!
- Oben: Schale ist innen mit dünnen Rippen verstärkt. Diese bewirken eine Wölbung des Bodens nach außen
- Unten: Schale mit dicken Rippen, so wölbt sie sich nach innen. Analog zur Platte treten auch hier wieder Einfallstellen gegenüber den Rippen auf.
-
Erkläre was du hier siehst!
- Wandstärkensprung: der dickere Teil schwindet stärker und der dünnere Teil verwirft sich.
- Sind solche Sprünge nicht zuvermeiden, empfiehlt es sich, einen fließende Übergang vorzusehen.
-
Erkläre was du hier siehst!
Wird eine dünnwandige Membrane von einem dickwandigen Ring umschlossen, so wird dieser stärker schwinden. Die Membrane wird sich ausbeulen
-
Erkläre was du hier siehst!
- trotz einer gleichmäßigen Werkzeugtemperierung ein starker Verzug zu erwarten
- Segment a nur schlecht gekühlt
- Segment b von zwei Seiten gekühlt und wird daher weniger schwinden als Segment a
- Winkel von weniger als 90° wird sich einstellen
-
Nenne Ansätze um der Eckengestaltung um Verzug vorzubeugen (7)!
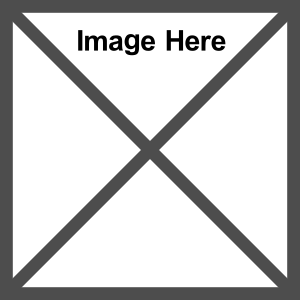 - 1: spitze Eckebei gleicher Wandstärke verrundet.Radius ausreichend groß
- 2: Wanddickenverkleinerung (evtl. aber Hinterscheidung)
- 3: Einfach herzustellende Wanddickenverkleinerung
- 4: Außenecke dank Innenfreistich erhalten
- 5: Verundung mit scharfer Außenecke
- 6: Innenseite stärker gekühlt
- 7: Kühlleistung durch hochwärmeleitfähige Einsätze im Werkzeug erhöht
-
Wie werden Toleranzen unterteilt?
- Fertigungstoleranzen
- Verarbeitungstoleranzen
- Betriebstoleranzen
-
Durch welche Faktoren werden Fertigungstoleranzen beeinflusst (6)?
- Abweichungen von der angenommenen Schwindungsberechnung
- Herstellungsbedingte formgebundene Werkzeugtoleranzen
- Herstellungsbedingte nicht formgebundene Werkzeugtoleranzen
- Verschleiß am Werkzeug
- Einfach- oder Mehrfachwerkzeug
- Lage und Art des Angusses
-
Durch welche Faktoren werden Verarbeitungstoleranzen beeinflusst (6)?
- Chargenunterschiede
- Feuchtigkeitsaufnahme während der Lagerung
- Nachschwindung
- Quellung durch Konditionierung
- Lageänderung beweglicher Werkzeugteile
- Einstellung der Maschine
-
Durch welche Faktoren werden Beriebstoleranzen beeinflusst (5)?
- Nachschwindung
- Temperaturänderung
- Quellung durch Konditionierung
- Feuchtigkeitsänderung
- Dehnung durch mechanische Beanspruchung
-
Welche Maße werden im Hinblick auf das Werkzeug unterscheiden?
- werkzeuggebundene Maße
- nichtwerkzeuggebundenen Maße
-
Was sind werkzeuggebundene Maße?
Was sind nicht werkzeuggebundene Maße?
- werkzeuggebunden: nur von einer Werkzeughälfte abhängig
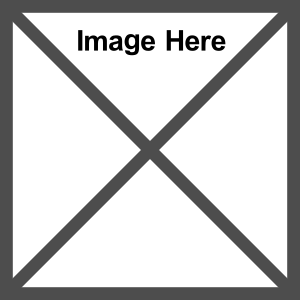 - nicht werkzeuggebunden: durch das Zusammenspiel mehrerer beweglicher Werkzeugteile
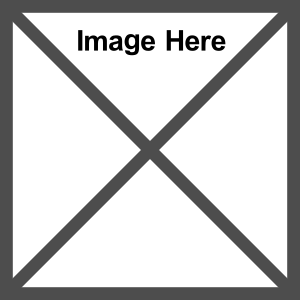
-
Welcher Grundsatz gilt bei der Wanddickengestaltung?
Worauf wirken sich Wanddicken aus (5)?
- Soviel wie nötig – so wenig wie möglich
- Formteilgewicht
- Realisierbare Fließweglängen
- Zykluszeit
- Toleranzen
- Qualität (Oberfläche, Lunker, Verzug)
-
Trage Wanddicken über erreichbare Fleißweglängen für übliche Thermoplaste auf (lciht, mittel und schwer fliessend)!
Nenne eine typische Anwendung!
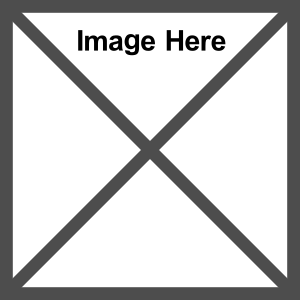 - Kabelbinder
-
Nenne Problem bei der Flächengestaltung und 3 Lösungsmöglichkeiten!
-
Nenne Problem bei der Rippengestaltung und drei Lösungsmöglichkeiten!
-
Vergleiche Rippen und Sicken!
(Nenne je 2 Vorteile)
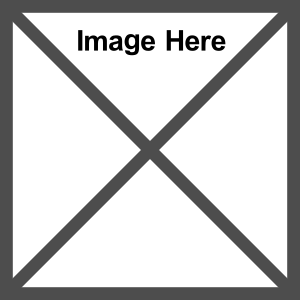 - Vorteile Rippen:
- Ebene Oberflächen realisierbar
- Bei Spritzguss Werkzeugaufwand geringer
- Vorteile Sicken:
- Um Faktor 1,8 steifer als Rippen
- Geeignet für Thermo- und blasgeformte Teile
-
Nenne Gestaltungsmöglichkeiten von Kreuzungspunkten und deren Eigenschaften!
-
Wie wirken sich folgende Kerbformen bei PC und wie bei ABS auf die Kerbschlagzähigkeit aus?
-
Wie können Grundkörper für Einschraubungen gestaltet werden (3)?
-
Was sind Gewindereinsätze?
Welche beiden Verfahren werden unterscheiden?
Wann eingesetzt?
- zur häufigen Lösung der Verbindung
- 2 Verfahren
- Mould-In-Technik
- After-Moulding-Technik
-
Wie sehen Gewindeeinsätze der Mould-In-Technik aus?
Eigenschaften und Einbringung?
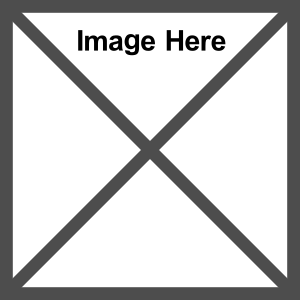 - Vor Herstellung in Form eingelegt, vom Kunststoff eingebettet
- genaues Positionieren der Einsätze im Werkzeug erforderlich
- überwiegend einseitig geschlossen
- genormt
-
-
Nenne Vor- und Nachteile von After-Moulding-Inserts gegenüber Mould-In's!
- Vorteile:
- Reduzierung der Zykluszeit (kein Einlegen erforderlich)
- keine Beschädigung des Werkzeuges durch Herausfallen beim Schließen
- Vermeidung von Spannungsrißbildung durch therm. Schrumpfung (kaltes Metall)
- kein Nachschneiden der Innengewinde beim Zusetzen durch Kunststoff
- Nachteile:
- zusätzliche Einsetzwerkzeuge oder automatische Zuführung erforderlich
- zusätzlicher Arbeitsgang zum Einbringen des Einsatzes
- zusätzlicher Transportaufwand
-
Nenne 3 unterschiedliche Schnappverbindungen!
|
|