-
What is a Particle?
- A useful working unit
- individual particle
- aggregate of many small individual particles (pellet, floc, etc.)
-
Typical Particle Size Ranges
Run-of-Mine < ____
Primary Crusher Product < _____
Secondary Crusher Product < _____
Rod Mill Product < ______
Ball Mill Product < ____
Flotation Feed < ____
- 1500 mm
- 150 mm
- 20 mm
- 6 mm
- 1 mm
- 0.5 m
-
Particle Sizing Methods (8)
- Sieve Analysis
- Sedimentation Methods
- Elutriation Methods
- Surface Area Methods
- Optical Microscopy
- Electrical Resistance Methods
- Laser Diffraction Methods
- Ultrasonic Methods
-
Factors Affecting Particle Sizing (3)
- Size
- Shape
- Specific Gravity
-
-
Sieve Analysis - Sieve Sizes
Mesh -______
Opening (aperture) Size - _______
- Mesh - number of openings per linear inch (100 mesh screen has 100 openings per inch)
- Opening (aperture) Size - function of mesh number and wire diameter.
-
Sieve Analysis - Standard Sieve Series
U.S. (ASTM) Standard - ____
Tyler Standard -____
- U.S. (ASTM) Standard - based on a 1 mm opening for an 18 mesh screen
- Tyler Standard - based on a 74 μm opening for a 200 mesh screen.
- Note: The screen aperture sizes in a complete sieve series are related by (2)¼. In practice, it is common to use every other screen in a complete series (i.e., √2). The smallest sieve available in either series is 400 mesh (37 μm).
- Example:
- 14 mesh = 1•(2)½= 1.41mm
- 16 mesh = 1•(2)¼= 1.19 mm
- 18 mesh = 1 mm
- 20 mesh = 1/(2)¼= 0.84 mm
- 25 mesh = 1/(2)½= 0.71 m
-
Sieve Analysis - Operating Concerns
Major Operating Concerns:
Screening Time (Probability of particle____)
Sample Weight (Probability of particle _____)
Typical Operating Values (Ball Mill Product):
Screening Time - ___minutes
Sample Weight - ____ grams
Other Operating Concerns:
____- ______.
___ of ___-
This problem is usually solved by ___ screening.
Dry screening is generally not appropriate below approximately 200 mesh
- Major Operating Concerns:
- Screening Time (Probability of particle passing through opening)
- Sample Weight (Probability of particle hitting another particle)
- Typical Operating Values (Ball Mill Product):
- Screening Time - 20 minutes
- Sample Weight - 500 grams
- Other Operating Concerns:
- Blinding - near mesh particles plug holes
- Adherence of Fines - fine particles stick on coarse particles. This problem is usually solved by wet screening.
- Dry screening is generally not appropriate below approximately 200 mesh
-
Sedimentation - Stokes’ Law
-
Stokes’ Law Example
A quartz sphere (ρ s= 2.65 g/cm 3) falls in a column of distilled water at 25°C (µ = 0.01 g/cm•s (poise), ρ = 1.0 g/cm3). What is the diameter of the sphere if it falls 20 cm in 30 minutes?
-
Sedimentation Methods:
Two-Layer Methods -introduce sample on top of liquidand monitor particle concentrationat some other level
Homogeneous Suspension -disperse particles in liquid andmonitor concentration change
Incremental Method -density change monitored:(1) at a fixed depth as f(time)(2) at a fixed time as f(depth
- examples:
- Andreasen Pipette
- Photosedimentometer
- X-Ray Sedimentometer
Cumulative Method -the rate at which material settlesout of suspension is monitored
- examples:
- Sedimentation Balance
- Sedimentation Colum
-
Elutriation - Size Separation
- a process of sizing particles by means of an upward current of fluid, usually air or water.
- Infrasizer - air
- Cyclosizer - water
-
Surface Area Methods
- infer particle size from specific surface area
- Gas Adsorption
- Gas Permeability
- Gas Diffusion
-
Microscopy
- Optical Microscopy (> 1 µm)
- Scanning Electron Microscopy (> 0.001 µm)
- may require the use of 2-D to 3-D conversion methods
- linked with automatic image analysis
-
Electrical Resistance
- -based on change in resistivity as particle passes between two electrodes (counts and sizes)
- -accurate, good resolution, requires skilled operator, applicable from 1 to 400 µm
- -Coulter Counter
-
Laser Diffraction
- particle size distribution is related to the diffraction of laser light as the beam passes through a suspension of the sample
- Honeywell Microtrac
-
Ultrasonics
- measurement depends on the varying absorption of ultrasonic waves in suspensions of different particle sizes
- Autometrics PSM System (on-line)
-
Potential Problems in Size Analysis
- improper screening of fines
- lower detection limits
(Note: Both problems can be detected in the size distribution plot, and both problems can be corrected by adjustments to the size distribution plot or material balancing of the size data.)
-
Purpose of Size Distribution Equation
- A convenient way to represent large quantities of data
- A means of characterizing the size of a material
- A basis for comparing sample
-
Size Distribution Equations
- Gaudin-Schuhmann Equationz commonly used in mineral processing
- generally fits fine particle distributions, such as ball mill product
- tends to fit best below the 75-80% passing size
- Rosin-Rammler Equation
- commonly used in coal preparation
- generally fits coarse particle distributions, such as those used for dense media separation in coal preparation plants
- relatively linear over the entire range of particle sizes
-
The Gaudin-Schuhmann Equation
Y = (x/k)^m
- Y = cumulative fraction finer than x
- x = particle size
- k = size modulus (theo max particle size)
- m = distribution modulus (spread of dist)
logY = m * log(X) - mlog(K)
-
The Rosin-Rammler Equation
Y = 1-exp(-(x/x') n))
- Y = cumulative fraction finer than x
- x = particle size
- x' = size modulus
- n = distribution modulus
-
Importance of Crushed Stone Quality
- Over 1 billion tons of crushed stone produced per year.
- Commonly used in concrete, asphalt, road base, construction filler, etc.
- Quality parameters most important for end use.
- Quality specifications often set by federal and state regulations (DOT)
-
Types of Quality Parameters (8)
- Size and Size Distribution
- Shape
- Specific Gravity
- Permeability
- Abrasion and Degradation Resistance
- Impact Strength
- Weathering Resistance
- Presence of Fines
-
Size and Size Distribution
- Size Gradations
- Aggregate sizes designated by weight percent ranges in specific size classes
- Coefficient of Uniformity
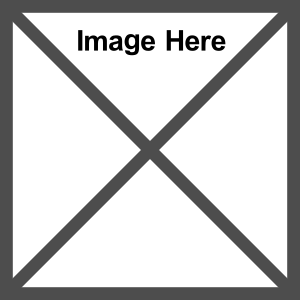 - Cu> 6: dense or well graded; wide size range; desirable for maximum strength and stability.
- Cu< 4: uniformly or open graded; narrow size range; high permeability
-
Shape - a major parameter affecting quality of end products:
flat and elongated particles ______
angular particles ____
rough-textured particles provide _____
can reduce strength of asphalt and concrete when load is applied to the thin side
increase shear strength of mixtures and skid resistance of pavements over rounded particles
better bonding with cement or road materials.
-
Shape - Flatness and Elongation
- Flatness - width/height from an end view
- Elongation - length/width from a top view
-
Shape- percent voids
used as indirect measure of fine particle shape (related to packing
-
Specific Gravity
Apparent Specific Gravity-
Bulk Specific Gravity-
Bulk Specific Gravity (saturated, surface dried)
- Apparent Specific Gravity
- ratio of the dry aggregate weight to the volume of the aggregate excluding any permeable pores.
- Bulk Specific Gravity
- ratio of the dry aggregate weight to the volume of the aggregate including all permeable and impermeable pores.
- Bulk Specific Gravity (saturated, surface dried)
- ratio of the saturated aggregate weight to the volume of the aggregate including all permeable and impermeable pores.
-
Permeability
- Let
- A = dry weight of sample
- B = weight of surface dried, water saturated sample
- C = weight of water saturated sample
- Water Absorption (%) = (B-A)/(C-A) x 10
-
Abrasion and Degredation
The slow degradation of a material resulting in the creation of a few large pieces of rock (as opposed to “wear”, which results in the creation of many small particles).
In concrete production, degradation during mixing alters the original gradation of the material.
In pavements, degradation can lead to unstable bedding layers causing pavement cracking
Los Angeles Degradation Test (LA Abrasion)
-
Impact Strength
Page Impact Test
-
Weathering Resistance
Sulfate Soundness Test
-
Presence of Fines
Atterberg Limits:
Liquid Limit-
Atterberg Limits
Liquid Limit (LL) - the water content at which a sample of -40 mesh material passes from the plastic to liquid state.
Plastic Limit (PL) - the lowest water content at which a sample of -40 mesh material remains cohesive enough to hold together when rolled with the fingers on a glass plate into a “thread” of 1/8”diameter.
- Plasticity Index (PI) = LL - PL
- Low PI is desirable
-
What is Comminution?
- Particle Size Reduction
- Purpose:
- liberate minerals (most common)
- reduce particle size (crushing)
- produce material of a controlled particle size (crushed-stone production)
- increase surface area (chemical processing)
-
Magnitude of Comminution
Energy Consumption:
Steel Consumption (Wear):
Total Energy Consumtion
Over 1.5 billion tons of ores and rocks are comminuted annually in the U.S.
- Energy Consumption
- Total Energy Consumption - 10-20 kwh/ton
- Primary Crushing - 0.25 kwh/ton
- Secondary Crushing - 0.55 kwh/ton
- Rod Mill Grinding - 5.4 kwh/ton
- Ball Mill Grinding - 5.7 kwh/ton
- Steel Consumption (Wear)
- Total Steel Consumption - 1.8-2.5 lb/ton
- Grinding Rods - 1.2 lb/ton
- Grinding Balls - 0.9 lb/ton
- Crusher Liners - 0.03 lb/ton
- Mill Liners - 0.2 lb/ton
- Total Energy Consumption
- 33 billion kwh (including energy associated with steel consumption)
- 1.5% of the total U.S. output of electricity (1978)
- 40-75% of direct operating costs for mineral processing
-
Comminution Energy Fundamentals
Possible courses of energy:
- Size Reduction Energy
- -Material Being Broken
- ---Lattice rearragements
- ---Surface Energy
- ---Elastic Deformation - Heat
- ---Plastic Deformation -Heat
- -Communition Machine and Interparticle effects
- ---Friction -Heat
- ---Kinetic Energy
- ---Electrical Effects
- ---sound
-
Communition Efficiency
- If surface energy is only form considered useful - 0.1-1%
- If lattice rearrangements are considered part of the breakage process - 1-2%
- If elastic and plastic deformation are considered part of a necessary precursor to breakage - 20-50%
-
Modes of Fracture
- Rapid Compression - impactors and tumbling mills
- Slow Compression - crushers and tumbling mills
- Abrasive Shear - crushers and tumbling mills
- Tension - 1/10 of compressive strength; no available commercial method (Spin rock - F. Bond)
-
Novel Methods of Comminution
- Steam or Chemical Expansion (tensile)
- Microwave Heating (heat stressed)
- Ultrasonic
-
Comminution Laws
A method of relating Energy Consumption to Size Reduction
Useful in design of comminution devices
- Three basic “laws” of comminution:
- Rittinger’s Law (1867)
- Kick’s Law (1885)
- Bond’s Law (1951)
-
-
-
Bond’s Law
-
Practical Form of Bond’s Law
Let Wi(Bond Work Index) equal the energy (kwh/ton) required to break a material from infinite size to 80% passing 100 µm.
-
Liberation
- Physical detachment of minerals from one another
- One of the major objectives of comminution
- Maximize liberation at coarsest possible particle size
-
Modes of Fracture (2)
- Transgranular - fracture across grain boundaries
- Intergranular - fracture along grain boundaries
-
Particle Composition Types
Free (or liberated) - a particle consisting of only one mineral type
Locked (or middlings) - a particle consisting of more than one mineral type
-
Degree of Liberation
The percentage of a given mineral occurring as free particles in an ore in relation to the total content of that mineral.
- D.O.L. =
- 100 * (weight of free particles in mineral A)/(free particles" + weight of locked particles in min A)
-
Methods of Determining Optimum Mesh of Grind
Direct - Degree of Liberation (Gaudin)
Equivalent number of locked particles
Consider five particles containing 5%, 50%, 25%, 90% and 30% of mineral A, respectively. The equivalent number of locked A is 0.05 + 0.50 + 0.25 + 0.90 + 0.30 = 2.00
-
Locking Factor:
Gives additional weight to underestimated locked particles since locked particles can appear as free under a microscope, but free particles can never appear as locked.
-
Differential Liberation
Separate or discard some material at a coarse size and regrind the remaining material to produce a concentrate (save on grinding costs).
-
Limitations of Energy/Size Relationships
- Based on only one particle size (e.g., 80% passing size)
- Unable to predict the effect of operating variables on grinding circuit performance
- Complete size distribution needed for simulating subsequent processes
-
Probability Model of Comminution
-
Components of K(Selection Function)
Selection Function (S) - the probability that particles in a given size range will be selected for breakage (Diagonal Matrix).
-
Components of K(Selection Function (cont.))
-
Breakage Function
Breakage Function - the manner in which particles distribute after breakage
-
Open-Circuit Ball Mill Model
-
Kinetic Model of Comminution
- Consider grinding to be analogous to a chemical reaction having a reaction rate constant, k.
- Consider M1to represent the mass of material in the top size class in the mill.
- Assuming this is a batch ball mill and all material that breaks must leave size class 1, the change of mass in size class 1 is given by
dM 1/dt = -k 1M1
-
Kinetic Model of Comminution
(Breakage Rate Function)
-
Kinetic Model of Comminution(Breakage Distribution Function)
Breakage Distribution Function (b ij) - the fraction of broken particles of size class j which report to size class i
-
|
|