-
Wie sieht ein Laserbearbeitungskopf aus (Skizze + Beschriftung)?
-
Welche Aufgaben hat der Laserbearbeitungskopf?
- Fokussierung der Laserstrahlung auf das Werkstück durch eine über der Schneiddüse angeordnete Linsen- oder Spiegeloptik
- Zufuhr des Schneidgases koaxial zum Laserstrahl an die Bearbeitungsstelle zum Austrieb des geschmolzenen bzw. verdampften Werkstoffes aus der Schnittfuge
-
Wie groß ist der Abstand zwischen Düsenaustritt und Werkstück i.d.R. zu wählen und warum?
- klein 0.5mm - 1mm
- um einen guten Werkstoffaustrieb aus der Schnittfuge zu gewährleisten
-
Welche Laserstrahlschneidarten unterscheidet man und welches Kriterium dient zur Unterscheidung?
- Nach Zustand des Fugenwerkstoffs nach Prozess
- Dampf: Laserstrahlsublimierschneiden
- Flüssigkeit: Laserstrahlschmelzschneiden
- Oxidationsprodukt: Laserstrahlbrennschneiden
- meist Vermischung dieser
-
Was für Vorgänge gibt es beim Laserstrahlsublimierschneiden?
Welche Werkstoffe? Was ist beim jeweiligen Werkstoff zu beachten?
- Werkstoff im Bereich der Schnittfuge verdampft und entweicht mit hoher Geschwindigkeit
- Holz, Papier, Keramik und Kunststoffe, die keinen ausgeprägten schmelzflüssigen Zustandbesitzen: unter Schutzgasatmosphäre damit keine Oxidation (Verbrennen)
- Metalle: Laserstrahlintensitäten so hoch und die Einwirkzeiten so kurz zu wählen, dass das Schmelzvolumen minimal ist
-
Nenne Vor- und Nachteile des Laserstrahlsublimierschneidens!
- Vorteile:
- alleinfalls kleine Schmelzfilmdicken => glatte Schnittkanten
- kleine Wärmeeinflusszone (WEZ), geringe Wärmebelastung => venachlässigbare thermomechanische Wirkung
- keine Oxidation der Schnittkante => Weiterbearbeitung ohne Nachbehandlung
- insesondere bei Werkstoffen ohne ausgeprägten Schmelzpunkt
- Nachteile:
- hohe Intensitäten erforderlich => leistungsstarker Laser mit hoher Strahlqualität
- Materialdicke darf Laserstrahldurchmesser nicht wesentlich überschreiten, da Materialdampf sonst an Schnittwand kondensiert und Fuge zusetzt (nur bei Werkstoffen mit flüssiger Phase)
-
Was für Vorgänge laufen beim Laserstrahlschmelzschneiden ab?
- Werkstoff durch den Laserstrahl im Bereich der Schnittfuge in den schmelzförmigen Zustand überführt und die Schmelze mit einem Gasstrahl ausgetrieben
- Material muss nicht verdampft werden => höhere Schnittgeschwindigkeiten als beim Sublimierschneiden
-
Welche Schutzgase werden beim Laserstrahlschmelzschneiden verwendet?
inerte Gase wie Stickstoff oder Argon
-
Nenne Vor- und Nachteile des Laserstrahlschmelzschneidens!
Welche Stoffe möglich?
- Vorteile:
- geringer Energiebedarf zum Aufschmelzen des Werkstoffs
- keine Oxidation der Schnittkanten
- Trennen unterschiedlicher Materialien möglich (Gläser, Kunststoffe, Metalle)
- Nachteile:
- genaue Anpassung der Schneidgasparameter
- komplexere Verfahrensführung durch die erforderliche Hochdruck-Schneidgasströmung
- chrakteristische Riefen und Bartbildung an Ausgangsseite durch Schmelzströmung
- hoher Schneidgasverbrauch
-
Welche Laser werden vorwiegend zum Laserstrahlschmelzschneiden verwendet?
CO2-Laser und Nd:YAG- Laser im cw- und Pulsbetrieb
-
Wodurch ist die Dicke des Schmelzfilms beim Laserstrahlschmelzschneiden limitiert?
durch die Wärmeleitung in das Werkstück und die Begrenzung der Oberflächentemperatur auf die Verdampfungstemperatur
-
Warum kann beim Laserstrahlschmelzschneiden eine bestimmte Schnittgeschwindigkeit nicht überschritten werden?
Mit zunehmender Schneidgeschwindigkeit muss ein wachsender Massenstrom durch einen in seiner Dicke begrenzten Schmelzfilm ausgetrieben werden
-
Wodurch steigt bzw. sinkt der Schneidwinkel beim Laserstrahlschmelzschneiden?
Der Neigungswinkel der Schneidfront sinkt mit der Schneidgeschwindigkeit und steigt mit der Laserstrahlintensität
-
Was ist bzgl. der Laserstrahlschneidbarkeit von Aluminium zu sagen?
- Reinaluminium ist schwierig zu schneiden, da Reflexion des Laserstrahls sehr hoch
- Absorptionsgrad liegt bei CO2-Lasern nur bei 1-2%, bei Nd:YAG-Lasern bei ca. 7%
- Wärmeleitfähigkeit und Wärmekapazität sind relativ groß
- Je höher die Legierungsanteile im Aluminium, desto besser die Schneidbarkeit des Werkstoffes
-
Erkläre die Vorgänge beim Laserstrahlbrennschneiden!
- Analog zum Schmelzschneiden wird beim Brennschneiden das Werkstück im Bereich der Schnittfuge erhitzt und die Schmelze mit einem Gasstrahl ausgetrieben
- Durch die exotherme Reaktion des Sauerstoffs mit aufgeschmolzenem Metall erfolgt eine zusätzliche Energiezufuhr in den Wechselwirkungsbereich
-
Nenne Vor- und Nachteile des Laserstrahlbrennschneidens!
- Vorteile:
- größere Schneidgeschwindigkeiten (2- 6 mal größer als beim Schmelzschneiden)
- geringerer Gasdruck
- Nachteile:
- Oxidation der Schnittkanten
- Gefahr des Materialabbrandes
-
Wodurch kann der Materialabbrand beim Laserstrahlbrennschneiden verhindert werden?
- geeignete Prozessführung:
- Pulsbetrieb
- Reduzierung des Schneidgasdruckes
-
Wozu wird das Laserstrahlbrennschneiden hauptsächlich eingesetzt?
fast ausschließlich zum Trennen von Metallen, vor allem unlegierten und niedriglegierten Stählen, eingesetzt
-
Welche Energieverluste gibt es beim Laserstrahlbrennschneiden?
- benötigte Energie wird über Laserstrahlung und exotherme Reaktion des Werkstoffs mit dem Prozessgas (Reaktionsenergie) zugeführt
- Verlsute infolge der Reflexion der Laserstrahlung am Werkstück und durch Wärmeleitung in das umliegende Material
-
Wie läuft die Oxidation von bsplsw. Eisen beim Laserstrahlbrennschneiden ab (grob)?
- stufenweise Oxidation des Eisens unter Bildung mehrerer Zwischenprodukte
- Jede diese Reaktionen ist exotherm und gibt Wärme ab
-
Wodurch kommt die Instabilität des Schneidprozesses beim Laserstrahlbrennschneiden zustande?
- Schwankung der Temperatur
- Dicke der Oxidschicht wächst => höherer Widerstand gegen Oxidation => Abbremsen des Schneidprozesses => Sinken der Temperatur
- Sobald bestimmte Dicke der Oxidschicht erreicht, fällt diese ab und Temperatur steigt wieder an
-
Welche Vorteile bietet das Laserstrahlschneiden gegenüber den konventionellen Schneidverfahren?
- hohe Prozessgeschwindigkeiten
- geringe Wärmebelastung, verzug- und spannungsfreies Trennen
- hoheRechtwinkligkeit und Ebenheit mit geringer Riefigkeit
- bei Verwendung von Schneidgas keine Oxidation
- Nachbearbeitung nur bei hohen Anforderungen notwendig
-
Nenne die 5 Hauptgruppen der Parameter, die den Laserstrahlschneidprozess maßgeblich beeinflussen!
- Laserstrahlparameter
- Schneidgas
- Werkstück
- Handhabung
- Optik
-
Nenne einige Laserstrahlparameter (6)!
- Wellenlänge
- Intensitätsverteilung
- Strahlqualität
- Strahldurchmesser
- Polarisation
- Leistung (cw, gepulst)
-
Nenne Schneidgasparameter (4)!
- Gasart
- Gasdruck
- Düsenform
- Düsenabstand
-
Nenne Werkstückparameter (3)!
- Material
- Dicke
- Oberflächenzustand
-
Nenne Handhabungsparameter (2)!
- Schneidgeschwindigkeit
- Kopforientierung
-
Nenne Optikparameter (3)!
- Brennweite
- Fokuslage
- Abbildungseigenschaften
-
Wie sollte ein Laserstrahl für Schneidaufgaben polarisiert sein und warum?
- zirkular, damit die Absorption in jeder Bewegungsrichtung des Bearbeitungskopfes gleich ist
- Eine lineare oder elliptische Polarisation führt zu Kantenfehlern und Fehlern in der Rechtwinkeligkeit des Schnittspalts
-
Nenne Anwendungsmöglichkeiten zur Laserbearbeitung mittels Roboterapplikation!
- bei hohen Flexibilitätsanforderungen
- 3D-Bearbeitungsraum
- Schweiß- und Schneidapplikationen
-
Was wird beim Einsatz einer Roboterapplikation benötigt (Komponenten)?
- Festkörperlaser
- Strahlführung mittels Lcihtleitkabel
- Mitführen von Peripherieelementen => Schutzgasversorgung, Crossjet, Optikkomponenten
-
In welchen Fällen wird Laserbearbeitung mittels Scanneroptik genutzt?
- 3D-Applikationen
- kurze Schweißnähte (Steppnähte, Punktschweißen)
- schwierigere Zugänglichkeit
- hohe geforderte Flexibilität
- Robotereinsatz möglich
-
Wann werden Portalsysteme bei der Laserbearbeitung genutzt?
- CO2-Laser mit Verwendung von Strahlführungssystemen
- große Baudimensionen
- hohe Genauigkeit
- Verwendung auch als Rohr- oder Profilschweißanlagen
-
Welche Arten der Polarisation gibt es un welchem Bauteil im Laser kommt Aufgabe zu die Polarisation vorzugeben?
- Linear
- Zirkular
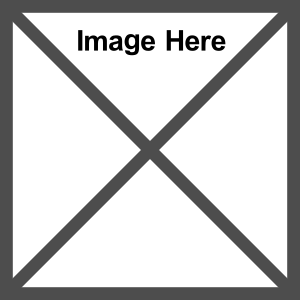 - Resonator gibt Polarisation vor
-
Was ist die Polarisation des Lichtes?
- Polarisationsrichtung gibt Richtung des elektrischen Feldvektors E relativ zu vorgegebener Achse an
- Natürliches Licht ist „unpolarisiert",das bedeutet, dass alle Richtungen des elektrischen Feldvektors mit gleicher statistischer Wahrscheinlichkeit vorliegen
- Laserstrahlung in der Regel linear polarisiert, das heißt der elektrische Feldvektor hat eine feste, definierte Richtung
-
Was hängt von der Polarisationrichtung ab, wenn man die Wechselwirkung mit Materie betrachtet?
Bei Reflexion bzw. Brechung linear polarisierter Strahlung an einer Grenzfläche hängen Reflexions- und Transmissionsgrad von der Polarisationsrichtung der Strahlung ab
-
Was ist der Brewster-Winkel?
Gibt den Winkel an, bei dem von einfallendem, unpolarisiertem Licht nur die senkrecht zur Einfallsebene (d. h. parallel zur Grenzfläche) polarisierten Anteile reflektiert werden. Das reflektierte Licht ist dann linear polarisiert.
-
Trage für diese Anordnung die maximal mögliche Schnittgeschwindigkeit über 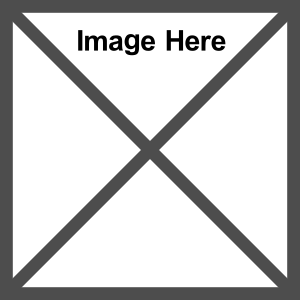 auf!
Was folgt für ein Schluss im Hinblick auf die 3D-Bearbeitung?
- Bei 3D-Bearbeitung zirkular polarisiertes Licht, damit Schnittqualität unter jedem Winkel gleich bleibt!
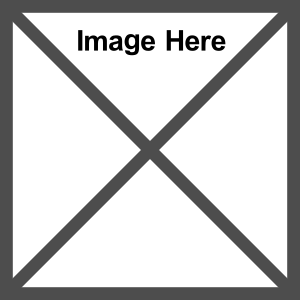
-
Mit welchen Effekten kann man Licht linear polarisieren?
Welche Bauteile setzen diese Effekte um?
- dichroitisches Filtern
- Doppelbrechung
- Reflexion
- Bauteile:
- Dichroitischer Polarisationsfilter
- Polarisationsprisma
- Brewsterplatten, Dünnschichtpolarisatoren
- λ/4- und λ/2-Plättchen
-
Was bedeutet Dichroismus?
Licht einer Polarisationsrichtung wird selektiv absorbiert
-
Was sind Brewsterplatten?
- Platte aus Glas wirkt polarisierend, wenn sie schräg in Lichtstrahl gestellt wird
- Beim Reflexionsgrad der Plattenoberflächen wird nach senkrechter (s) und paralleler (p) Polarisation unterschieden. Ist Einfallswinkel gleich Brewsterwinkel, wird die p-Komponente überhaupt nicht reflektiert, so dass reflektierte Strahlung vollständig s-polarisiert ist
- Brewsterplatte ist Polarisator mit geringem Wirkungsgrad (da s-Reflexionsgrad deutlich kleiner 100% ist)
-
Was sind λ/4- und λ/2-Plättchen?
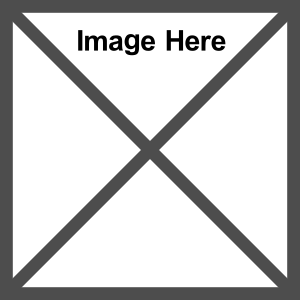 - λ/4-Plättchen:
- erzeugt zirkular polarisiertes Licht
- weisen Kristallachse in der Schichtebene auf => Richtung der linearen Polarisation der eingestrahlten Wellen muss unter 45° zu dieser Vorzugsrichtung stehen
- volle Wirkung kann nur für eine Wellenlänge erreicht werden
- λ/2-Plättchen:
- Zur Drehung der linearen Polarisation
- Durch Rotation des Plättchens kann die Richtung der Polarisation kontinuierlich verändert werden
-
Welche Fügeverindungen werden hinsichtlich der Geometrie der Fügefläche unterschieden?
- punktförmige
- flächige
- linienförmige
-
Welche Schweißverfahren werden unterschieden?
- Schmelzschweißverfahren
- Pressschweißverfahren
-
Wie unterteilt sich das Schmelzschweißen weiter (5)?
- Widerstandsschmelzschweißen
- Elektronenstrahlschweißen
- Lichtbogenschweißen
- Gasschmelzschweißen
- Laserstrahlschweißen
-
Nenne die zwei wichtigsten Pressschweißverfahren!
- Widerstandpressschweißen
- Reibschweißen
-
Wie lautet das Prinzip des Elektronenstrahlschweißens?
Nenne auch Wirkungsgrad und Leistungsmaximum!
- Elektronen im Hochvakuum durch Hochspannung beschleunigt
- Strahlbildung durch Triodensystem (Kathode, Steuerelektrode, Anode)
- Elektronen 2/3 Lichtgeschwindigkeit, bis 30kW Leistung
- kinetische Energie der Elektronen beim Aufprall in Wärme gewandelt
- bis 70% Wirkungsgrad
-
Nenne Vor (4)- und Nachteile (2) des Elektronenstrahlschweißens!
- Vorteile:
- Verbinden unterschiedlicher Metalle
- Hohe Schweißgeschwindigkeiten
- extrem tiefe, schmale, parallele Nähte
- geringer Wärmeeintrag
- Nachteile:
- Arbeitsfeld im Vakuum (sonst hohe Verluste)
- genaue Vorbereitung der Schweißfuge
-
Was wird durch das Vakuum beim Elektronenstrahlschweißen ermöglicht?
Schweißen hochreaktiver Werkstoffe
-
Wie lautet das Prinzip des Plasmaschweißens?
- Ionisierung von Plasmagasen (Argon) durch Hochfrequenzimpulse
- Hilfslichbogen (Pilotbogen) zwischen negativ gepolter Wolframelektrode und als Düse ausgebildeter Anode
- Plasmastrahl von Schutzgas umgeben, keine Oxidation
-
Beschreibe eine Prinzipskizze des Plasmaschweißens!
-
Nenne Vor- (4) und Nachteile (2) des Plasmaschweißens!
- Vorteile:
- feinste Nahtoptik
- Zusatzwerkstoffe nicht zwingend erforderlich
- hohe Schweißgeschwindigkeiten
- geringer Wärmeeintrag
- Nachteile:
- 2 Schutzgase nötig (Argon + Wasserstoff)
- keine Spaltüberbrückbarkeit
-
Nenne zum Plasmaschweißen geeignete Werkstoffe!
- Chrom-Nickel-Werkstoffe
- beschichtete und unbeschichtete Stähle
- Titan
- Nickel-Basis-Werkstoffe
-
Wie lautet das Prinzip des Wolfram-Inertgas-Schweißens?
Lichtbogenschweißen mit nicht verzehrender Elektrode unter Schutzgas mit entkoppelten Schweißzusatz
-
Nenne Vor- (4) und Nachteile (1) des Wolfram-Inertgas-Schweißens!
- Vorteile:
- sehr guter Schweißnahtschutz vor Sauerstoff
- saubere Schweißnaht
- kleine Wärmeeintragszone
- wenig Spritzer
- Nachteile:
- geringe Schweißgeschwindigkeit
-
Nenne für WIG-Schweißen geeignete Werkstoffe!
-
Wie lautet das Prinzip des Lichtbogenhandschweißens?
- Aufspannen eines Lichtbogens zw. Werkstück und Schweißelektrode
- hohe Temperatur des Lichtbogens bewirkt Aufschmelzen des Werkstoffs
- verzehrende Elektrode mit Ummantelung dient als Schweißzusatz und Oxidationsschutz
-
Nenne Vor- (4) und Nachteile (1) des Lcihtbogenhandschweißens!
- Vorteile:
- überall einsetzbar
- niedrige Anschaffungskosten
- leichte Handhabung
- Schlacke als Schweißnahtschutz
- Nachteile:Entfernung von Schlackespritzern
-
Nenne fürs Lichbogenhandschweißen geeignete Werkstoffe!
- unlegierte Stähle
- Stahlguss
- Gusseisen
-
Beschreibe eine Prinzipskizze des Lichbogenhandschweißens!
-
Wie lautet das Prinzip des Autogenschweißens?
- Metall durch Verbrennungsgase erhitzt
- Gasflamme schirmt Schweißbad gegenüber Umgebung ab (keine Oxidation)
- häufig Schweißdraht als Zusatzstoff verwendet
-
Nenne Vor- (3) und Nachteile (3) des Autogenschweißens!
- Vorteile:
- hochfest und dichte Verbindungen
- keine allzu aufwendige Nahtvorbereitung
- keine teure, störanfällige Technik
- Nachteile:
- breite Wärmeeinflusszone, hoher Verzug
- relativ langsam
- geringe Abschmelzleistung
-
Welche Werkstoffe sind Autogenschweißbar?
- unlegierte Stähle
- niedriglegierte Stähle
- Gusseisen
- Nichteisenmetalle
-
Beschreibe eine Prinzipskizze des Autogenschweißens!
-
Beschreibe das Prinzip des Widerstandspressscheißens!
- Energie durch Stromfluss über elektrischen Widerstand der Schweißzone
- Punktschweißen, Rollennahtschweißen, Abbrennstumpfschweißen
-
Nenne Vor- (4) und Nachteile (2) des Widerstandpressschweißens!
- Vorteile:
- kostengünstig, kleine Fügezeiten
- eist kein Schweißzusatz
- geringe Wärmeeinbringung und Verzug
- Schweißroboter können günstig genutzt werden
- Nachteile:
- hohe Oberflächengüte der Werkstücke nötig
- Stoßartige Strombelastung ungünstig für benachbarte Maschinen
-
Nenne fürs Widerstandspressschweißen geeignete Werkstoffe!
- legierte und unlegierte Stähle
- Messing
- Eignung des Werkstoffs abhängig von Schweißfaktor S
-
Beschreibe eine Prinzipskizze des Widerstandspressschweißens!
-
Wie lautet das Prinzip des Reibschweißens?
- beide Werkstücke fest eingespannt
- eins in Rotation versetzt und ans andere gepresst
- drehendes Werkstücke wird abgebremst und Anpressdruck erhöht, womit Reibschweißverbindung hergestellt wird
-
Nenne Vor- (3) und Nachteile (3) des Reibschweißens!
- Vorteile:
- kurze Schweißzeit
- verzugsarm durch symmetrische Eigenspannungen
- hohe Dauerschwingfestigkeit
- Nachteile:
- Durchmesser und Länge der Bauteile durch Maschinengröße begrenzt
- nur- quasi rotationssymmetrische Fügequerschnitte möglich
- hohe Maschinenanschafungskosten
-
Beschreibe eine Prinzipskizze des Reibschweißens!
-
Definiere Fügen!
Fügen ist das auf Dauer angelegte Verbinden von Werkstück geometrisch bestimmter Form mit formlosen Stoff
-
Welche Fügeverfahren sind mit einem Laser umsetzbar?
Definiere je!
- Schweißen:
- Vereinigen von Werkstoffen in der Schweißzone unter Anwendung von Wärme und/oder Kraft mit und ohne Schweißzusatz
- Löten:
- thermisches Verfahren zum stoffschlüssigen Fügen und Beschichten von Werkstoffen, wobei eine flüssige Phase durch Schmelzen eines Lotes (Schmelzlöten) oder Diffusion an den Grenzflächen (Diffusionslöten) entsteht. Schmelztemperatur des Grundwerkstoffes nicht erreicht
-
Nenne Einflussfaktoren auf die Laserschweißeignung von Werkstoffen!
- chemische Zusammensetzung
- metallurgische Eigenschaften
- physikalische Eigenschaften
-
Welche prinzipiellen Zusammenhänge gelten für die Laserschweißeignung von Stahl?
- hoher C-Gehalt: Aufhärtung, interkristalline Kristalle können auftreten ab C>0.2%
- hoher (S,P,Pb)-Gehalt: niedrig schmelzende Phasen (Eutektika) können an den Korngrenzen aufteten => nicht schweißbar (Heißrisse, Poren)
-
Nenne nicht laserschweißgeeignete Stähle (4)!
Nenne auch jeweils den Grund!
- Werkzeugstähle (zu hoher C-Gehalt)
- Automatenstähle (Zu hoher Gehalt an S,P,Pb)
- martensitische nichtrostende Stähle (Rissbildung in Naht)
|
|